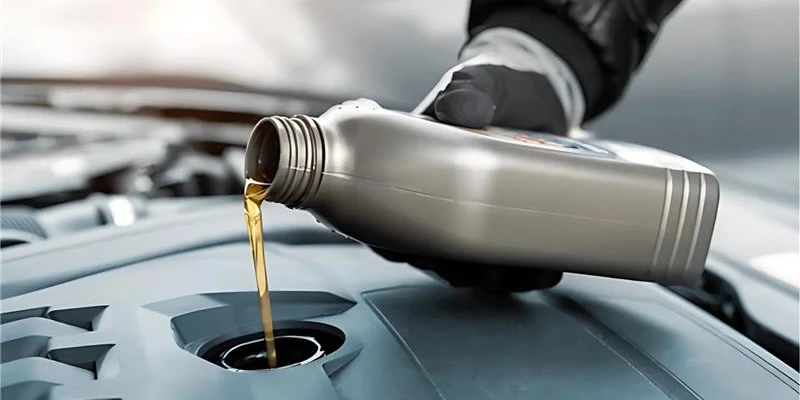
Additives emptying solution
Additives and raw base oil unloading from barrels in lube oil production
One leading lube oil manufacturer in India faced unique challenges in their barrel unloading operations, particularly in handling raw base oil and additives stored in underground tanks.
The customized NETZSCH NEMO Barrel Emptying System transformed the lube oil producer’s operations, addressing their challenges comprehensively. With enhanced process efficiency, significant energy savings, and reduced dependency on labor, the solution underscored NETZSCH's commitment to innovation and customer-centric solutions.
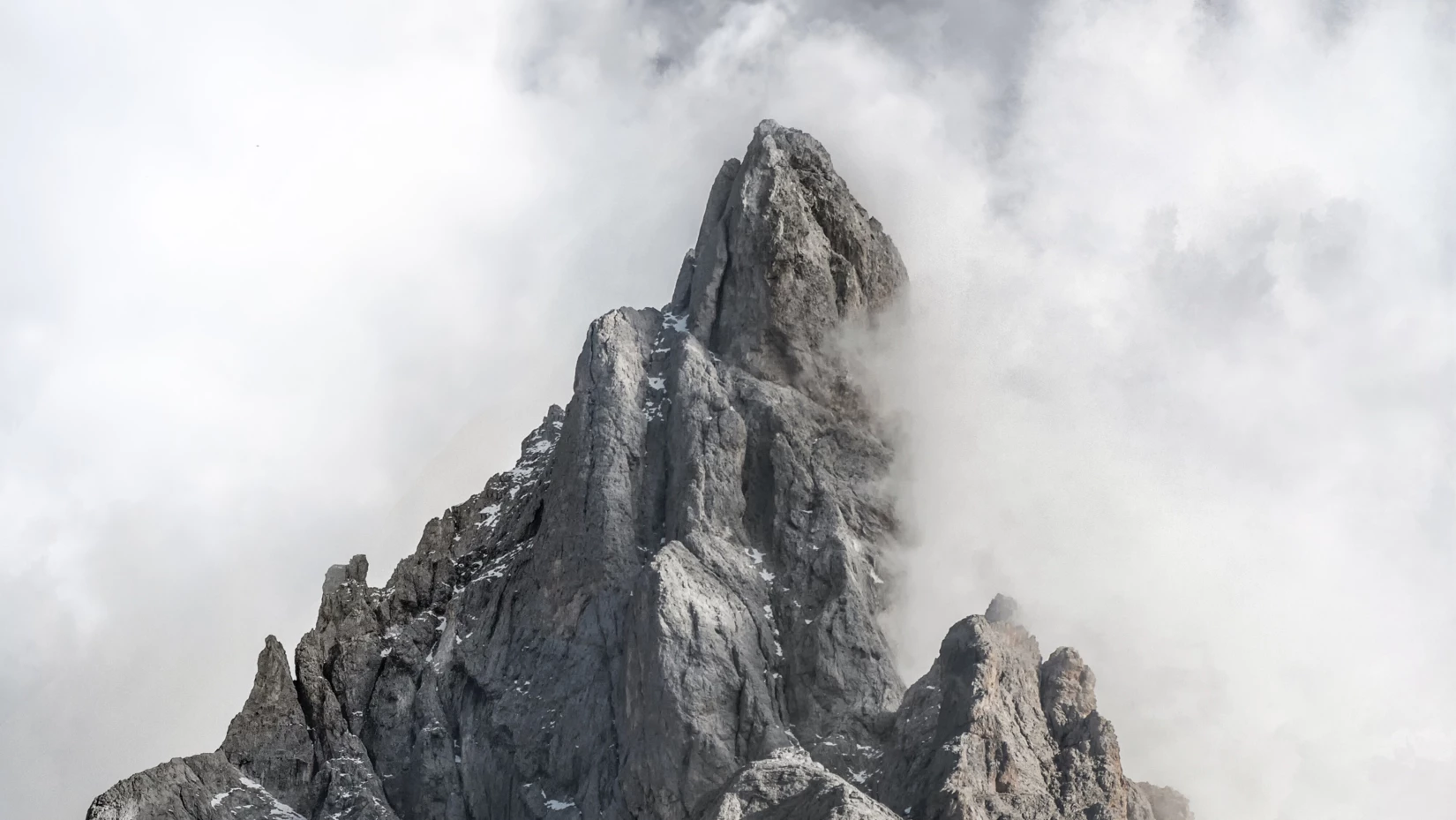
Individual Consulting
Existing Technology Challenges
Gear pumps were used to transfer the oil from underground to storage tanks situated on the second floor.
While this arrangement appeared functional, it was riddled with inefficiencies that significantly affected operations. Handling the additives having a very high viscosity of 80,000 cP, was difficult as the current pumps were unable to prime well. Hence its viscosity had to be lowered to 32,000 cP by preheating it before it could be pumped using the gear pumps. This pre-heating process consumed additional energy, introduced complexity to the workflow, and added to the operational costs.
The process was labor-intensive, requiring significant manpower for handling barrels. Workers needed to tilt the barrels from pallets manually and use forklifts to position them for unloading. This not only increased labor costs but also posed safety risks and extended process times. This manual dependence necessitated the need for a more automated and streamlined solution.
The underground tank storage posed several challenges and the most critical was the inability to use them during the rainy season due to flooding. This limitation disrupted the entire transfer process, causing operational delays and reducing overall efficiency. Without an alternative to the underground tanks, the manufacturer’s workflow was highly vulnerable to weather-related disruptions.
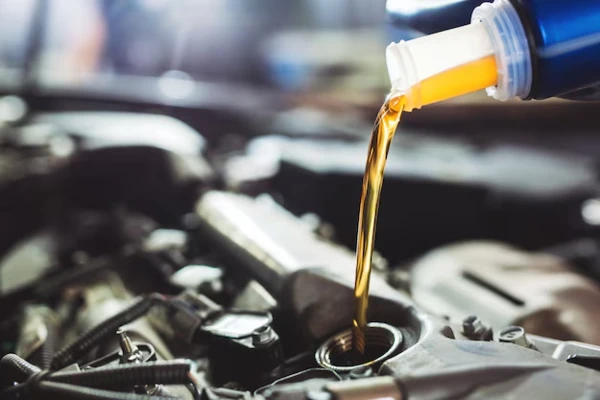
A drum pump equipped with a barrel emptying system
The NETZSCH ND Series drum pump with slim pump design was perfectly suited for closed barrels with spouts. This ensured seamless integration into the existing setup without the need for additional adjustments or investments in barrel modifications.
Another major benefit of the drum pump was its ability to handle high-viscosity additives smoothly. The previous requirement relied on pre-heating to lower the viscosity, the NETZSCH drum pump eliminated this step entirely by directly pumping the additive at its original high viscosity. This not only simplified the process but also reduced energy consumption and operational costs.
The drum pump directly transferred the medium bypassing the underground storage tanks altogether. Instead of routing the base oil and additives through the flood-prone underground tanks, the drum pump efficiently transferred them directly to the storage tanks on the second floor. This eliminated the reliance on underground tanks, ensuring uninterrupted operations even during the rainy season and reducing the risk of flooding-related disruptions.
The Automated Solution
NETZSCH’s barrel emptying system is designed as a custom automation setup, featuring a swivel arm arrangement with drafters. This advanced system brought significant improvements:
- Ease of Operation: The swivel arm enabled easy positioning of the drum pump for precise and efficient emptying.
- Reduced Manpower: Automation eliminated the need for manual barrel tilting and forklift handling, cutting down manpower requirements drastically.
- Process Efficiency: The direct pumping capability reduced transfer times and minimized product losses during transfer.
- Energy Savings: By bypassing gear pumps and underground tanks, the system saved power previously used to operate these components.
- Increased Reliability: The system provided consistent and reliable performance, even during the rainy season, ensuring uninterrupted operations.
This holistic approach not only optimized the manufacturer’s workflow but also underscored NETZSCH’s commitment to delivering tailored, high-performance solutions.
NEMO® Barrel Unloading Pump
- Medium: Additives & Raw base oil
- Delivery rate: 1,500 to 5,000 kg/h
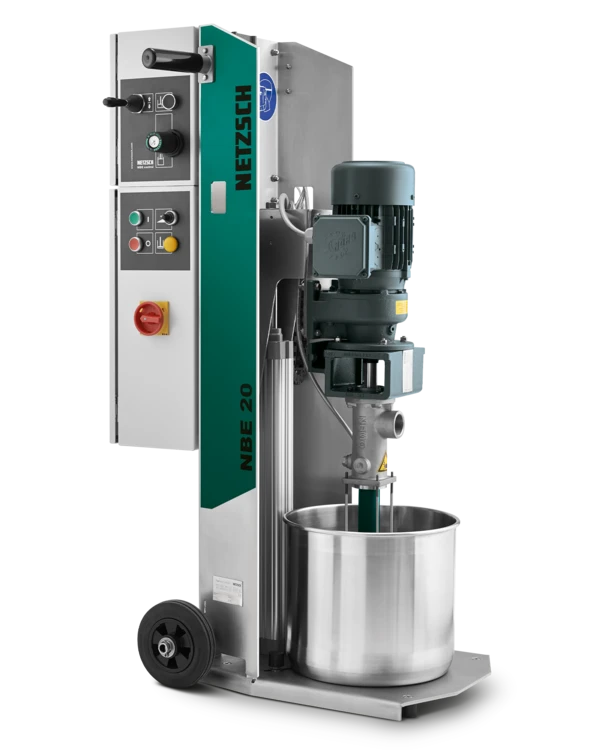