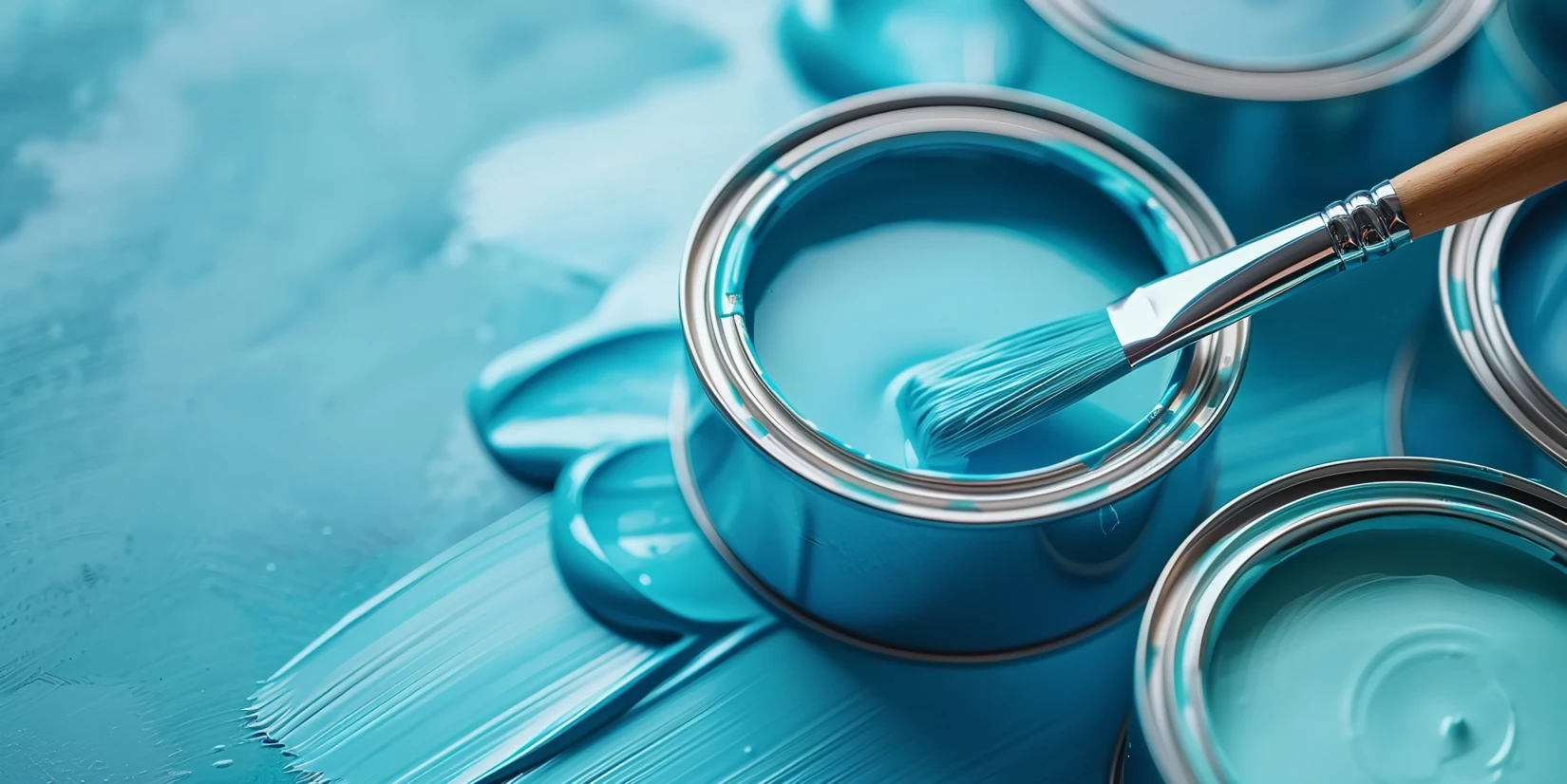
Offset paste ink transfer pump
Precision dosing solutions with NEMO® hopper progressing cavity pumps
Discover how NEMO® BF Hopper Pumps eased the paste ink, the highly viscous liquid transfer for an offset ink manufacturer.
Offset ink manufacturing involves handling of paste inks which are important in offset printing, a widely used printing technique. Paste inks are thick and viscous liquids that give optimal density and color for sharp and detailed prints.
A leading offset ink manufacturer faced operational difficulties in handling these highly viscous media manually. The process involved paste ink transfer from totes to blending tanks through chain hoists and tilters. Additives such as emulsifiers, color shades, and fillers were then added to the paste ink in the blender to achieve the desired ink consistency, specific color shades, viscosity, opacity, and drying time.
The operational challenge persisted till they find an optimized solution in the form of the NEMO® BF Hopper Pump with Force Feeding Screw, to deliver transformative results.
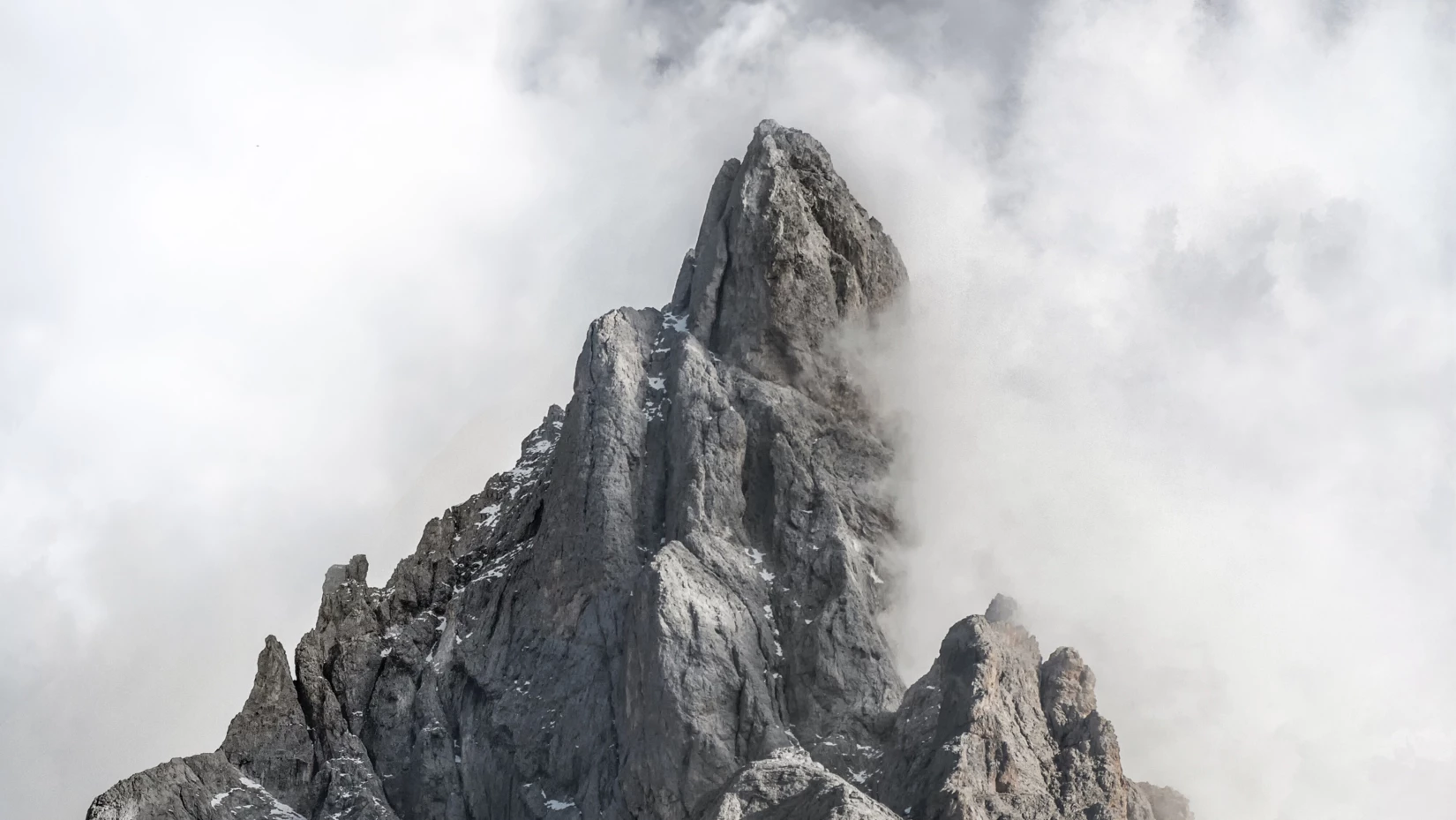
Individual Consulting

Paste ink transfer from totes to blending tanks
The manual process of paste ink transfer from storage totes to blending tanks involved multiple steps, each requiring careful coordination. First, the totes had to be moved from the storage area to the blending station. This was followed by attaching the tote to a chain hoist system and thereafter lift the heavy totes and positioning them over the blending tank. The totes were tilted using a tilter mechanism to pour the paste ink into the tank.
Furthermore, the manpower & physical effort involved in handling heavy totes posed potential safety risks, emphasizing the need for a more efficient and automated system. Manual handling of the highly viscous paste ink resulted in significant material wastage. The sticky nature of paste ink meant that residue remained in the totes leading to further losses. The entire operation, from moving the totes to completing the transfer, was time-consuming. These extended cycle times slowed down the production schedules.
The client was seeking an effective, automated solution to streamline the process, reduce material loss, and cut down on labour dependency.
Empty offset paste ink efficiently and reliably with this pump
After an in-depth understanding of the customer’s requirements and pain points, NETZSCH proposed the BF hopper progressing cavity pump as the ideal choice. This pump is known for its robust design and its ability to handle highly viscous, non-flowing, and sticky media. Equipped with a force-feeding screw, this pump ensures consistent feeding into the pumping elements, even for extremely challenging materials like paste inks.
The NEMO® BF progressive cavity design ensures the smooth transfer of paste ink without shear or material degradation. The pump’s-controlled operation eliminates spillage and wastage. Automation reduced the dependency on manual effort, cutting down manpower needs. Direct pumping from the storage totes to the blending tank streamlined the transfer, reducing overall process time.
NEMO® BF progressing cavity pump in industrial design
- Medium: Paste Ink
- Viscosity: 10,000 mPas
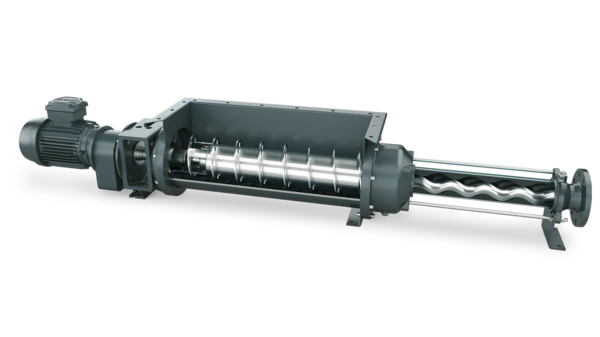