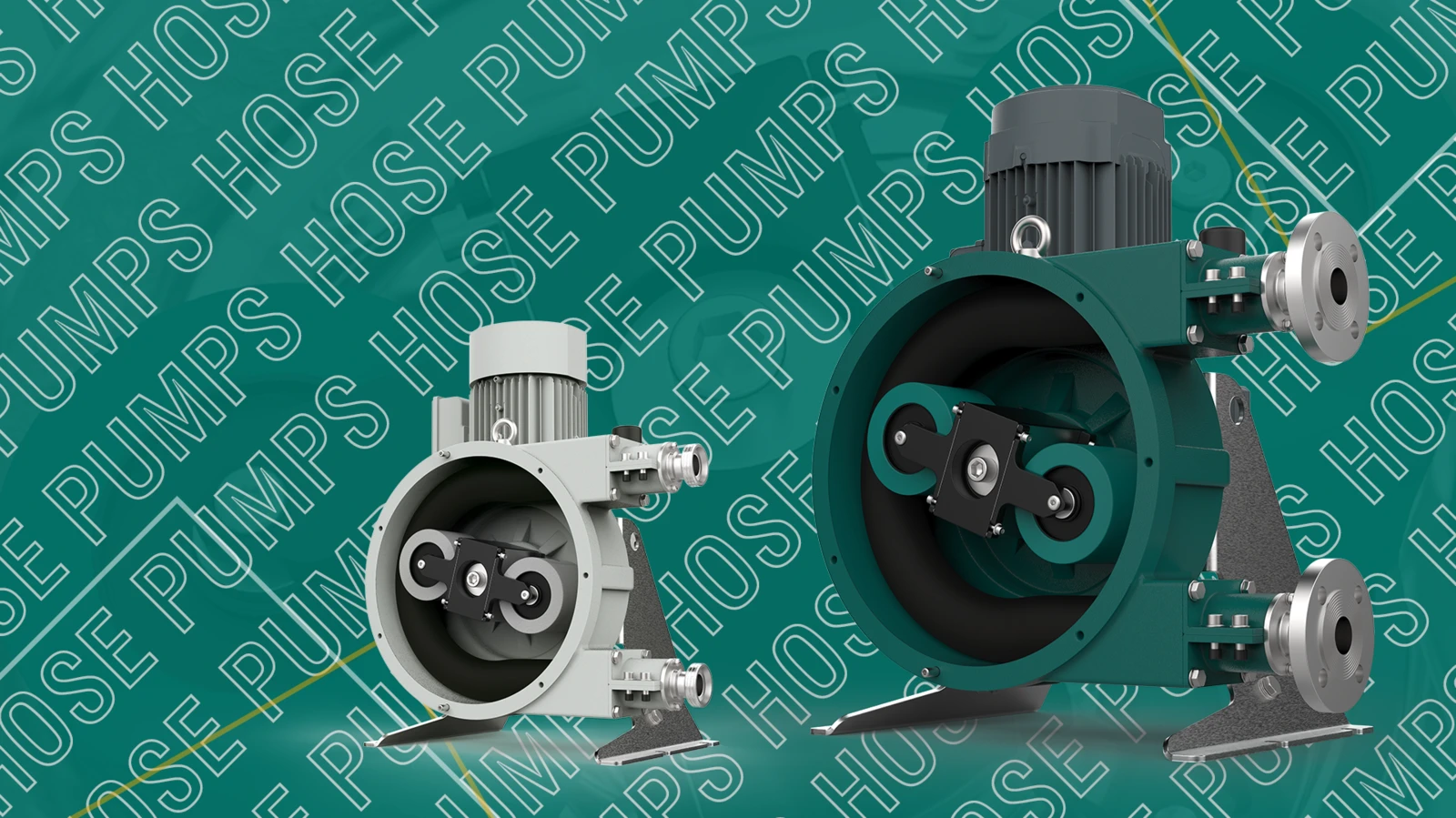
22.01.2024
Insights on Hose Pumps: A Buyers guide
Hose pumps, also known as peristaltic pumps, are an optimal pumping solution in various industries due to their unique operating principle and ability to handle challenging fluids. Whether in chemical processing, wastewater treatment, food, and beverage, or the ceramics/construction industry, choosing the right hose pump is crucial to ensuring efficiency, reliability, and cost-effectiveness. This guide will provide you the insights about hose pumps, their construction, working principle, applications and the key factors to consider when purchasing a hose pump.
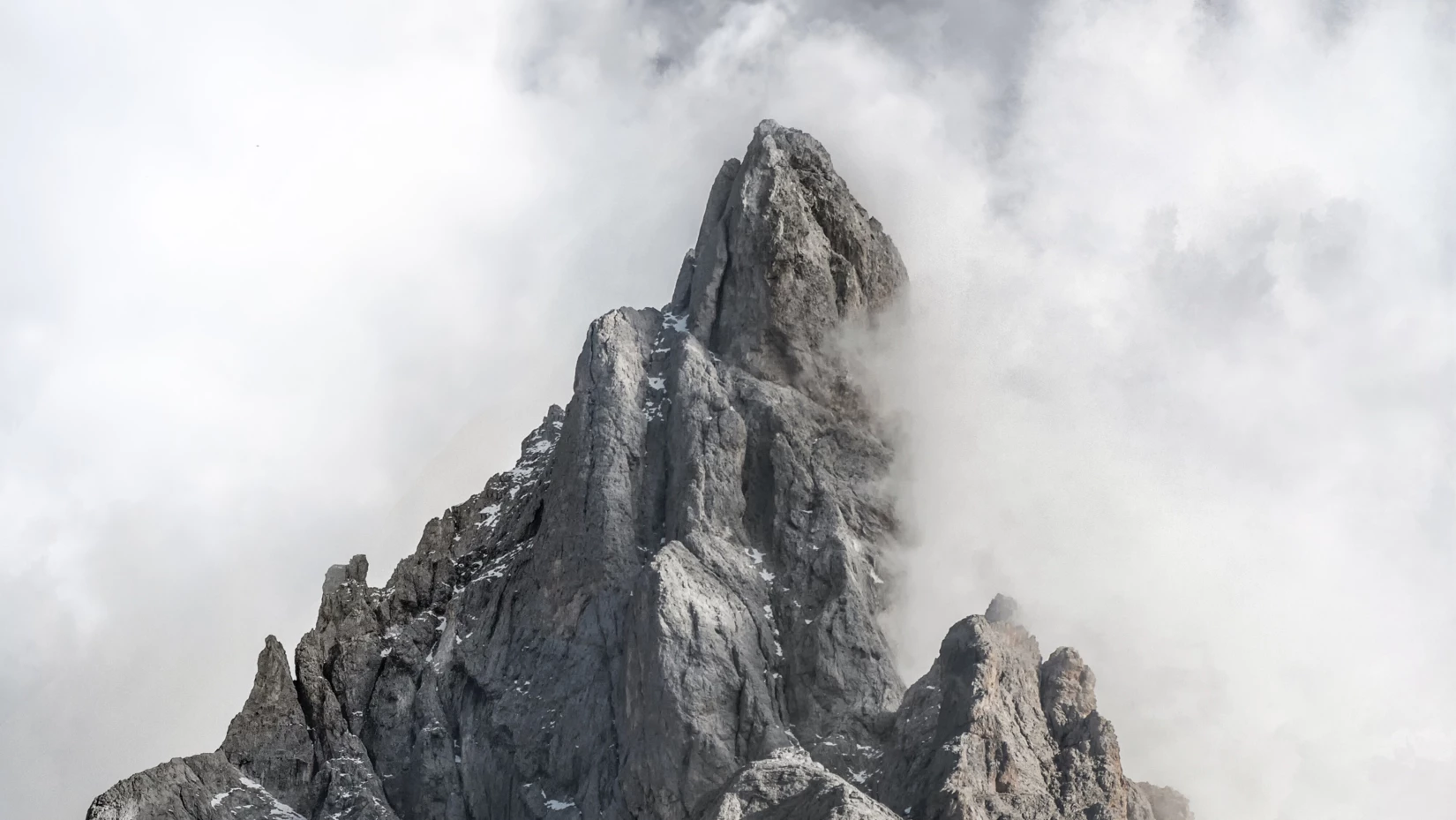
Customised Consulting
What are hose pumps?
Hose pumps operate based on the peristaltic principle, where a rotating set of rollers or shoes compresses a hose, creating a suction at the inlet to draw in the fluid and then pushing the fluid through it. This design offers several advantages, including gentle handling of the fluid, no contamination as the fluid only contacts the hose, and the ability to handle viscous, abrasive, or shear-sensitive materials.

How is a hose pump constructed?
Hose pumps consist of the following main components:
- Flexible hose
- Shoe or rotating roller mechanism
- Pump casing
- Drive system
- Inlet and outlet connections
- Openable front casing
The hose is the main component of the peristaltic hose pump. It is an elastomeric, flexible hose that is compressed by external pressure using a roller or shoe and afterward expands again. The hose can be made of various materials, such as rubber or thermoplastic elastomers. The Rotorrotor,Rotors,rotorsrotor or roller mechanism is responsible for the squeezing movement of the hose. This mechanism ensures that the hose is periodically compressed and released. The release at the suction end helps to draw the liquid through the vacuum generated. Thereafter the compression with the rollers enables constant liquid displacement. The pump housing encloses the flexible hose, Rotorrotor,Rotors,rotorsrotor or roller mechanism, and the bearings. It protects the components and allows the pressure and flow to be controlled. A motor or drive system moves the rotating element, the rotor which displaces the liquid. The hose pump also has inlet and outlet connections through which the medium to be pumped is introduced into the hose and discharged at the other end.
Where are hose pumps used?
- In wastewater treatment plants, hose pumps are ideal for dosing lime milk, activated carbon, sodium hypochlorite, ferric chloride and for conveying sludge & slurry, lime milk.
- In mining, for dosing cyanide, xanthate, reagents and to transfer minerals (thickener underflow), sludge & slurries.
- In ceramic & construction products, dosing of barium carbonate, potassium permanganate, additives, colorants, and in the transfer of cement, ceramic slurry/clay slip, high solid content products.
- In the food & beverage industry, dosing of additives, colors, flavors, diatomaceous earth (beer clarification) and conveys sauces, juices with fruits, feed filling machines, shear sensitive products. the sanitary variant of the hose pump offers you the highest level of hygiene and avoids contamination.
- In the chemical industry, for dosing pigments, water-based paints, resins & glues, detergents, acids, and corrosive products and to transfer abrasive products like titanium dioxide and difficult products such as latex. additionally, in scenarios where exotic metals are required in construction, such as when handling aggressive chemicals like hydrochloric acid, hose pumps offer a cost-effective alternative by avoiding the need for expensive materials. hose pumps are highly effective in situations where mechanical seals are problematic, as seen in applications like latex handling.
- Hose pumps also provide reliable performance in operations where dry running is unavoidable, such as pit emptying.
- Furthermore, they are excellent for the transfer of abrasive materials like silica slurry and are gentle enough to handle shear-sensitive liquids, including latex and emulsions.

What are the advantages of hose pumps?
- Seal-less Design: The absence of valves and mechanical seals minimizes maintenance needs, reduces the potential for leaks, and simplifies the overall design.
- Precision Dosing: Hose pumps provide highly accurate dosing, essential for applications requiring precise measurement and delivery of fluids.
- Versatility in Handling Viscous Fluids: They can manage a wide range of fluid viscosities, from 10,000 cps in smaller pumps to 25,000 cps in larger models, making them suitable for a broad spectrum of fluid handling tasks.
- Low Shear Handling: The gentle pumping action of hose pumps makes them ideal for handling shear-sensitive fluids, preventing damage to delicate materials.
- Minimal Contamination Risk: Since only the hose and nozzle are in contact with the fluid, there is a reduced risk of contamination, making these pumps ideal for applications where purity is critical.
- High Suction Capability: These pumps can create a strong vacuum (up to -0.95 bar), allowing them to lift fluids from depths of up to 9 meters, making them effective in applications requiring strong suction power.
- Dry Running Capability: Hose pumps can run dry indefinitely without damage, which is particularly useful in processes where fluid flow may be intermittent or inconsistent.
- Durability and Wear Resistance: Hose pumps are highly resistant to abrasion, enabling them to handle abrasive fluids without significant wear, which extends the pump's lifespan.
- Reversible Operation: Hose pumps can easily reverse flow direction, providing flexibility in various applications.
- Ease of Maintenance: With fewer moving parts and a simple design, hose pumps are easy to maintain, leading to lower operational costs and less downtime.
Low energy consumption
High dosing accuracy
High solid content
How to select right Hose pump?
Selecting the right hose pump involves careful consideration of various factors to ensure it meets your specific application requirements.
- Fluid Type: Assess the fluids chemical composition, viscosity, temperature, abrasiveness, and whether it contains solids. This will help to determine the appropriate hose material and pump design.
- Consider the performance envelope: Determine the required flow rate, pressure and temperature of your application. Ensure the pump can operate efficiently within your desired range without excessive wear or energy consumption.
- Right Hose Material: The hose material must be compatible with the fluid to prevent degradation and ensure a long service life. Common hose materials include:
- Natural Rubber: Suitable for general-purpose use and abrasive fluids.
- EPDM: Ideal for handling acidic and alkaline solutions.
- Nitrile: Best for oils, fuels, and hydrocarbons.
- Hypalon: Excellent resistance to chemicals, especially in aggressive environments.
- Hose Durability: Consider the hose’s durability, especially when dealing with abrasive or corrosive fluids, to minimize replacement frequency.
- Viscosity and solids Handling capability: Ensure the pump can handle the viscosity and solids content in the fluid. Hose pumps are effective for a wide range of viscosities, but lower viscosity is recommended for precise dosing.
- Suction Capability: If the application requires strong suction, choose a pump with a high vacuum capability. Hose pumps can create a vacuum up to -0.95 bar, making them suitable for lifting fluids from significant depths.
- Dry Running: If your process involves intermittent fluid supply, select a pump that can run dry without damage, a feature hose pumps naturally provide.
- Ease of Maintenance: Choose a hose pump that is easy to maintain, with accessible parts and simple hose replacement processes to reduce downtime.
- Cost Efficiency: Consider the total cost of ownership, including initial cost, energy consumption, maintenance, and hose replacement frequency. A more expensive pump may offer lower operating costs over time, making it a more cost-effective choice in the long run.
- Automation: Determine if your application would benefit from automated features such as variable speed drives, remote monitoring, or integration with process control systems. These features can enhance efficiency and provide more precise control over the operation.
- Expertism and service network: Procuring from a reputed manufacturer to discuss your specific needs. They can offer expert advice, recommend suitable models, and provide support in selecting the best hose pump for your application.
By carefully evaluating these factors, you can select a hose pump that meets your specific application requirements, ensures reliable performance, and offers a long service life.
Where to buy hose pumps?
NETZSCH Pumps & Systems has been engineering, developing, and producing positive displacement pumps worldwide for over 70 years. The particularly robust and maintenance-friendly PERIPRO® Peristaltic hose pumps from NETZSCH are suitable for aggressive and abrasive media with a solids content of up to 70 percent. At the same time, they offer you an extremely high suction capacity with minimal maintenance requirements. We promise you Proven Excellence - Outstanding Performance in all areas.
You're wondering whether the hose pump technology is the right one for your application?
No problem! We will collaborate with you to find the right pump solution for your problem.
As a global specialist in handling complex media, NETZSCH offers you numerous other pump technologies such as progressing cavity pumps, rotary lobe pumps, multi screw pumps, barrel emptying and grinding systems - you got the application, we provide the solution!