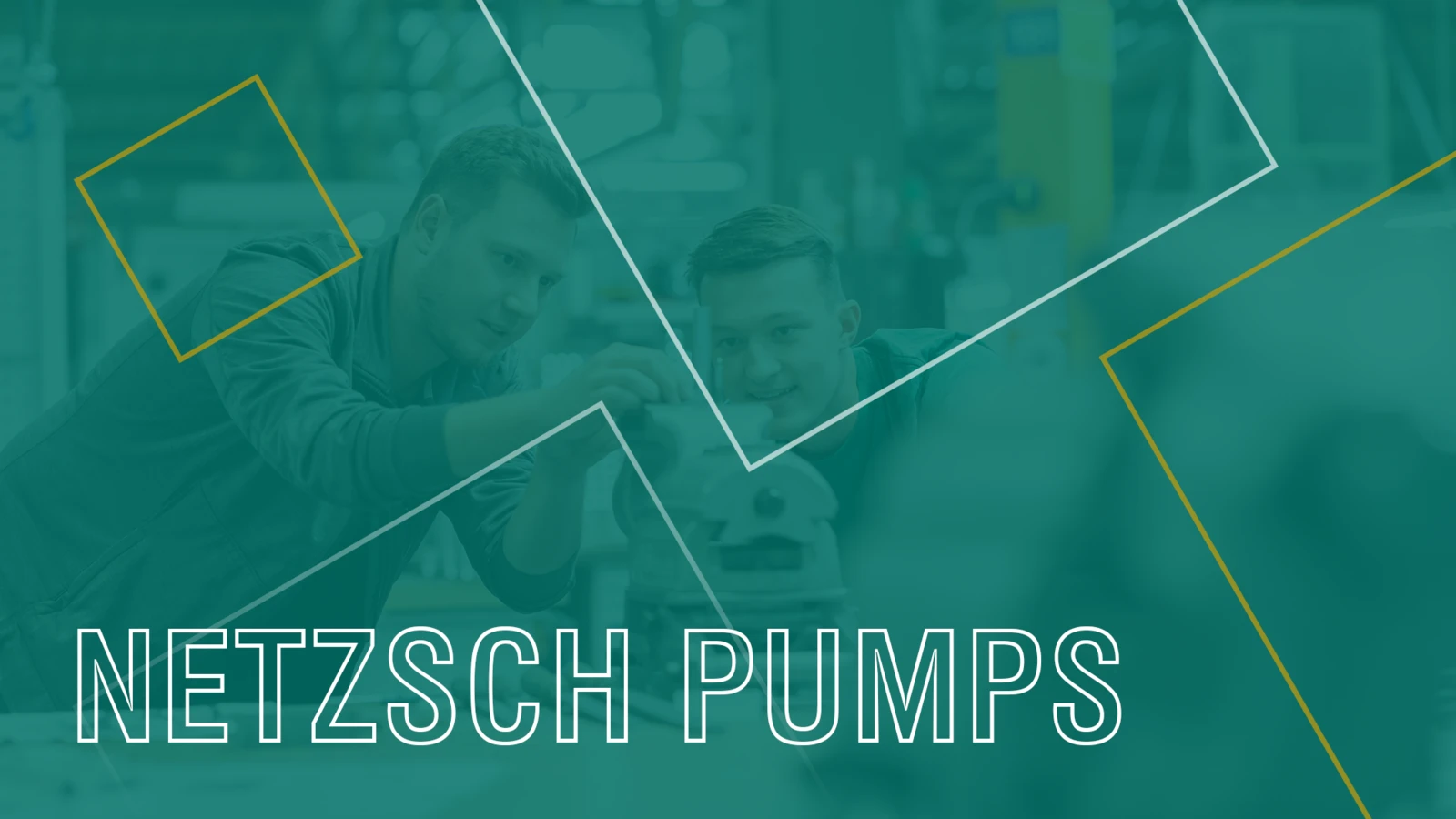
27.03.2024
Guide from Experts: How to Choose the Right Positive Displacement Pump for Your Application
Positive displacement pumps are the ideal pump solution for many applications in various industries, designed to draw a fixed amount of fluid and positively displace it into discharge pipe or system. The positive displacement pumps transfer a specific volume with each cycle or rotary or reciprocating movement as per the pump technology. These pump technologies as they create a good amount of vacuum during at the suction end of the pump, are good with priming and also drawing and conveying viscous liquids.
Their versatility allows them to be used across various industries, from oil and gas to food processing, wastewater treatment plants, biogas industry, chemical industry, and paper and pulp industries, where precise flow control and high-pressure output are essential.
Understanding the capabilities of different types of positive displacement pumps, which are broadly classified as rotary and reciprocating, is key to selecting the right pump for your specific application. Each pump type offers unique advantages and is suited for particular operational needs, ensuring optimal performance and reliability in even the most demanding environments.
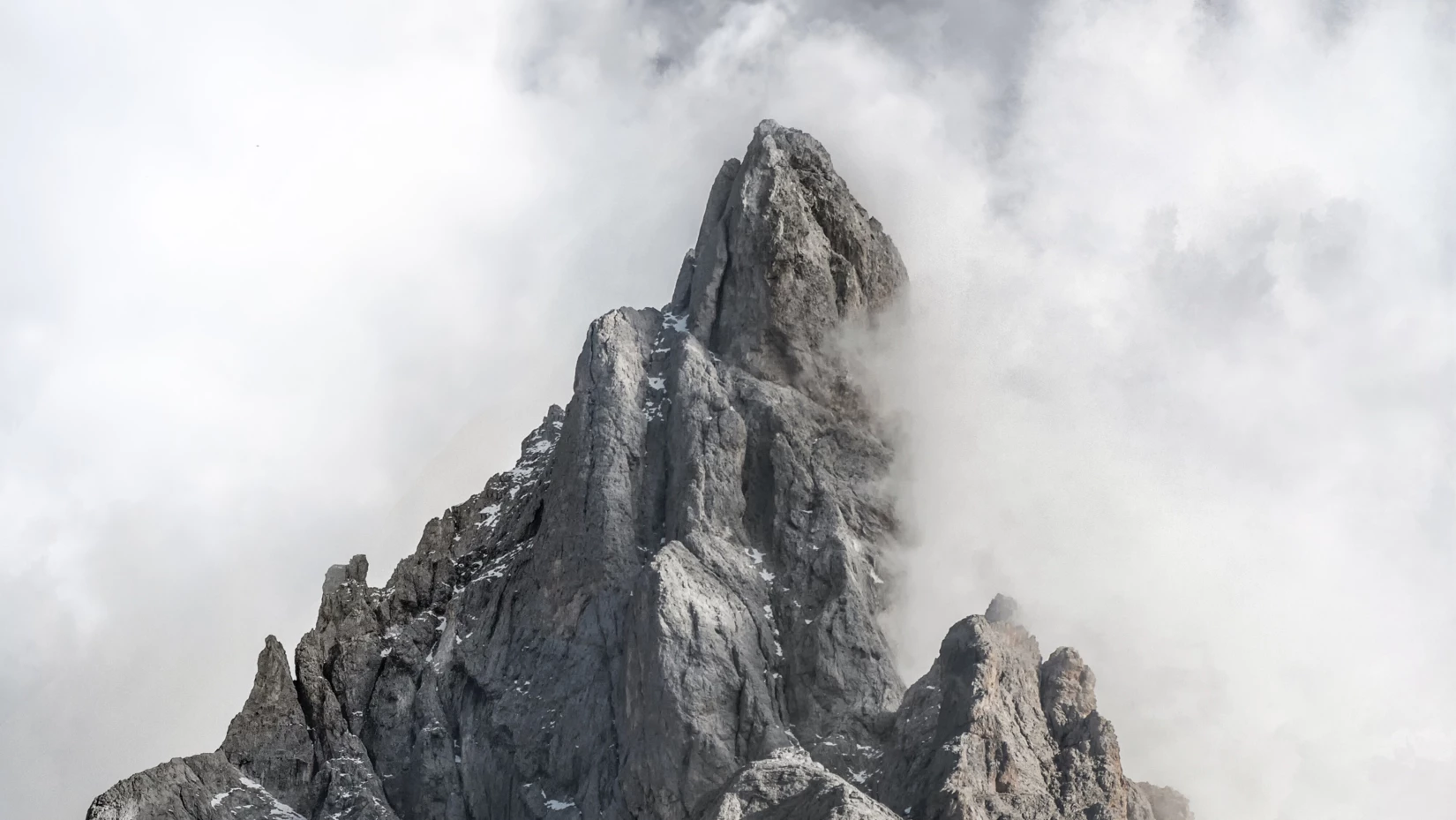
Customised Consulting
Positive Displacement Pump Types
Mostly all types of positive displacement pumps include a mechanism that falls into two classes relying upon the sort of movement of the pumping element. These two classifications of PD pump motion types are called reciprocating pumps and rotary pumps. Each category has different pump technologies, each suited to various kinds of applications, based on liquid properties and the pumping conditions.
- Reciprocating Pumps: Reciprocating pumps use a piston or diaphragm to move fluid. Common types include Piston Pump, Diaphragm Pump, and Plunger Pump.
- Rotary Pumps: Rotary pumps move fluid through the rotation of their internal components. Common types include Gear Pump, Rotary Lobe Pump, Screw Pump, Peristaltic Hose Pump, and Vane pump.
Parameters to Consider While Choosing a Positive Displacement Pump
Choosing the ideal positive displacement pump is important for efficient and reliable operation in any industrial application. Good understanding of the different types of PD pumps and their capabilities and limitations is vital to make the right choice. There are broadly two areas to consider which are the Fluid Properties and Pump Installation and duty conditions. You can make an effective decision that ensures optimal performance and longevity of your pump system. Here are the primary factors to consider:
Fluid Characteristics
- Viscosity: The viscosity of the fluid can significantly impact pump performance. High-viscosity fluids require pumps that can handle increased resistance and maintain consistent flow rates. The suction conditions have to be carefully considered based on the priming ability of the pump technology. The seal type if used is also critical to ensure good priming.
- Temperature: The thermal condition of the fluid has an influence on the fluid physical properties at the time of pumping. They also affect the pump materials that come in contact with the fluid. The limits of the pump components are to be considered. Temperatures up to 160 degrees can be well handled in pumps that have elastomers in their pumping elements. Temperatures higher than those are better suited with pumps that use only metal components.
- Abrasiveness: Conveying fluids that are laden with solids can be abrasive in nature. The abrasive nature of the fluid depends on the nature of the solids, % of solids, and the size of the solids. The management of the abrasive fluid during pumping to have minimum impact on the pump elements can be done by managing the fluid velocity, utilizing the right material combination of the pumping elements, and also using technologies that provide of best wear resistance.
- Corrosion: Liquids that are corrosive would have to be dealt with by selecting the right materials for the wetted parts of the pump. In cases of equipment that have to be operated under very critical conditions like remote field operations, the wetted parts should have the right corrosion allowance as well.
- Shear Sensitive: Liquids in different industries have to be conveyed along with preserving their physical property that can change due to shear. Selection of the right pumping technology that has the least amount of shear on the fluid, while being able to deal with the other properties of the liquid is critical for the right pump.
Flow Rate & Pressure Requirements
- Flow Rate: Determine the required flow rate for your application. The pump should be capable of delivering this flow consistently. The max, min, and nominal flow range during the operation is necessary to select the suitable pump type. It is important to understand the flow range for dosing applications to both select the right pump technology and the drivers.
- Pressure: The influence of pressure is on both the suction and the discharge end of the pump. Selecting the pump for the right suction conditions is crucial for trouble-free operation for both the pump and the liquid. It is critical to ensure the NPSHa is always greater than the NPSHr by the pump selected, in all installation conditions such as flooded suction, negative suction, and as well as conditions to draw liquid from vacuum tanks. It is also important to have the right estimation of the discharge pressure from the system. In certain process conditions using safety equipment like pressure relief values the safety valve relief pressure is also crucial. This information influences the selection of the drive as well as the pump size for the right fluid properties.
Material Compatibility
- Pump Materials: Select materials that are compatible with the fluid to prevent corrosion, wear, and contamination. Common materials include stainless steel, cast iron, and various polymers. There are pump technologies that offer full metal or full polymer of the right combination that is best suited for the thermal, mechanical , and chemical effect that can come on the pump.
- Seal Materials: Ensure the seals are compatible with the fluid to prevent leaks and extend pump life. There are pump technologies that are also seal-less for very specific applications that demand them.
Installation and Space Constraints
- Size and Footprint: Consider the physical space available for the pump installation, ensuring it fits within the designated area without interfering with other equipment. The selection of the right pump technology for the installation space available is critical. This is also very important to consider the ease of maintenance as a factor when one has to dismantle and service a pump. There are technologies that can be service in place without having to remove the pipe line .
- Mounting and Orientation: Some pumps require specific mounting orientations or additional support structures, which should be considered during selection.
Maintenance and Reliability
- Ease of Maintenance: Choose a pump with accessible parts and a simple design to facilitate routine maintenance and reduce downtime.
- Durability and Lifespan: Consider the expected lifespan of the pump and its components, particularly in demanding or continuous operation environments.
Compliance and Standards
- Industry Standards: Ensure the pump meets relevant industry standards and regulations, particularly in industries like food and pharmaceuticals where hygiene and safety are critical.
- Certifications: Look for pumps with certifications that indicate they meet specific quality and performance benchmarks.
PD Pump Type
- Rotary Pumps: Ideal for handling high-viscous, shear-sensitive, abrasive fluids and provides smooth, continuous flow. Common types include progressing cavity, lobe, peristaltic, gear, and vane pumps.
- Reciprocating Pumps: Best suited for applications requiring precise flow control and high-pressure output. Types include piston, plunger, and diaphragm pumps.
- There are several applications overlaps within the two groups and technologies. Hence it is important to consult us for the right recommendations for the pump technology keeping in consideration of the investment, operation costs, and other aspects such as maintenance to be the optimum.
NETZSCH Pumps & Systems India – Manufacturer of Rotary Positive Displacement Pumps
NETZSCH Pumps & Systems is a globally recognized specialist in complex fluid management, design, and manufacture four types of rotary positive displacement pumps, offering innovative pumping solutions tailored to a wide range of industrial applications. With over 7 decades of experience, and a strong commitment to quality, NETZSCH has built a reputation for delivering pumps that combine precision, durability, and efficiency.
The NETZSCH Product portfolio includes TORNADO® rotary lobe pumps, NEMO® progressing cavity pumps, PERIPRO® peristaltic hose pumps, NOTOS® multi-screw pumps and Grinders each engineered to handle the most challenging fluids, from highly viscous and abrasive substances to shear-sensitive and corrosive materials.
NETZSCH pumps are renowned for their reliability and robust construction, making them the preferred choice in industries such as oil and gas, chemical processing, food and beverage, and wastewater treatment. Our focus on innovation and sustainability ensures that the pumps are not only efficient but also environmentally friendly, with designs that minimize energy consumption and reduce operational costs.
Whether your application requires precise dosing, high-pressure delivery, or the ability to handle complex fluid characteristics, NETZSCH Pumps & Systems India provides customized solutions that meet the highest standards of performance and reliability. With a global network of aftermarket service and support, NETZSCH is dedicated to helping you find the right pump for your specific needs, ensuring smooth and efficient operation in even the most demanding environments.
As a global specialist in conveying complex media, NETZSCH's portfolio includes rotary lobe pumps, multi-screwpumps, peristaltic pumps, grinding systems, and barrel emptying systems as well as progressing cavity pumps.
Thanks to numerous models, we cater to various applications in a wide range of process industries. Whether environment & energy, chemical, pulp & paper, food & pharmaceuticals, mining, oil & gas upstream, mid- / downstream or batteries: We develop a customized and sophisticated progressing cavity pump solution for your enquiry.