
18.02.2025
Biogas Pump Solution for Recycling Food Waste
Biogas company leverages NETZSCH experience for their organic waste treatment and recovery applications
A pioneering biogas company embarked on an ambitious plan to transform its business model by leveraging advanced technologies, adding new recovery processes, and increasing its on-site treatment capacity. The upgraded and expanded plant features state-of-the-art bio-methanization facilities that produce biogas for energy generation along with valuable residues, including biofertilizers. Bio-methanization includes several processing stages: material reception, grinding and mixing, hydrolysis, anaerobic digestion, and gas management.
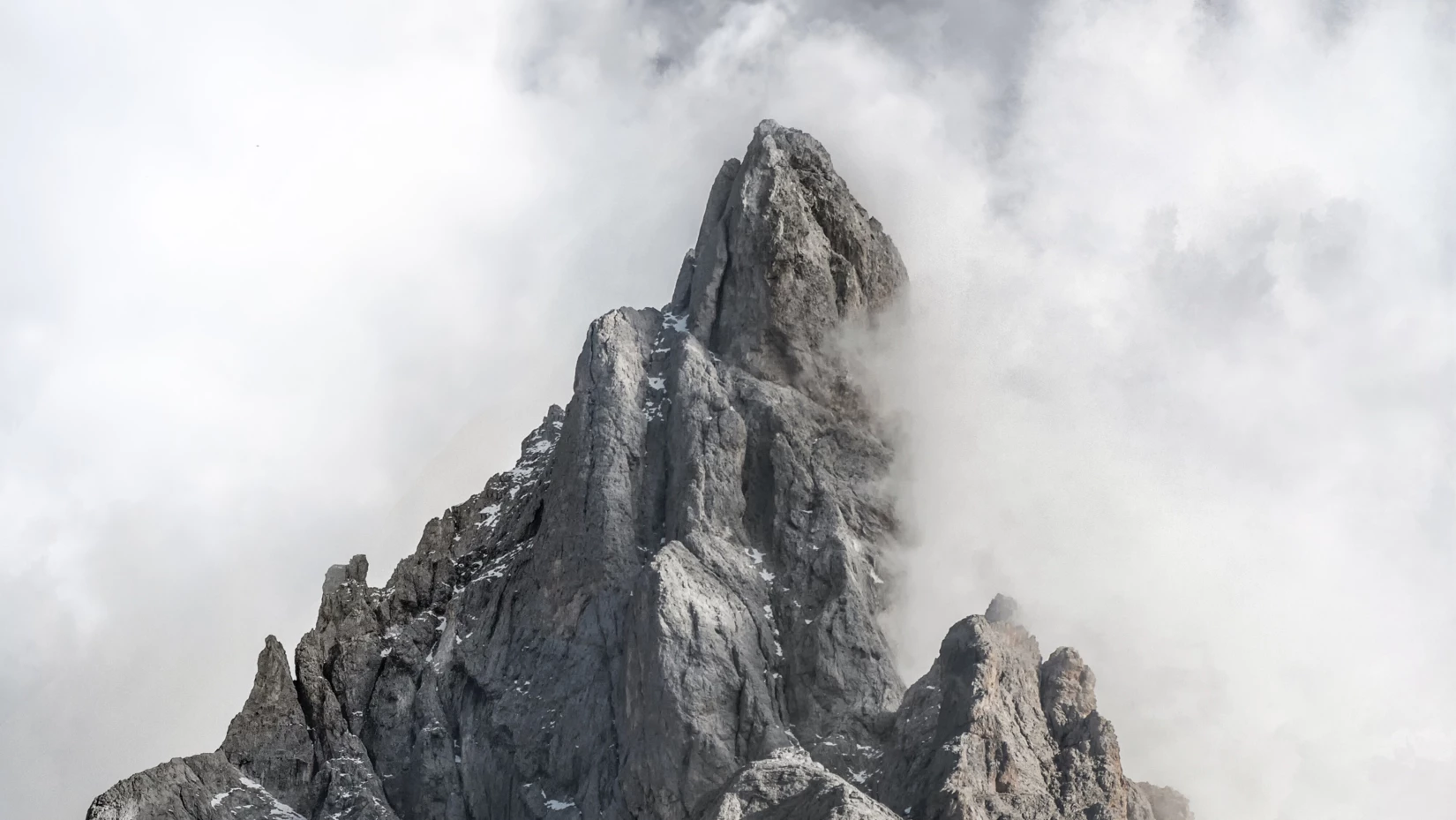
Customised Consulting
Recycling Food Waste
At the core of this company’s expansion is the reception of food waste as an additional feedstock. Recycling food waste stands out as a highly beneficial solution for the environment. Not only does it reduce reliance on fossil fuels for energy and fertilizer, but it also reduces landfill waste.
When food waste is discarded in landfills, it decomposes and emits methane, a harmful greenhouse gas. Although bio-methanization of food waste also generates methane, the process securely captures and manages the gas to avoid its release into the environment.
High Volume Reception within a Very Constrained Space
The Company had difficulty designing a system that could fit within the limited space available in their material reception area and reliably keep up with the expected influx of waste trucks arriving with a variation of food waste from grocery stores, restaurants, and food production facilities.
The initial design involved a complex, multi-stage process with limited capacity, excessive space, and substantial maintenance difficulties, potentially hindering the facility's ability to efficiently manage the influx of waste trucks arriving with food waste.
Complex Analysis of Operating Requirements
During the design process, the Company approached NETZSCH for pumping, mixing & grinding solutions after using NETZSCH pumps and macerating equipment in different processes in their facility.
NETZSCH technical experts collaborated closely with the company to understand the overall system requirements. They analyzed the operating parameters to calculate the precise liquid flow rate and the optimal mixing ratio between the organic solids and the liquid substrate used to feed the digesters.
This analysis was challenging due to the significant variability in the volume and composition of organic material arriving at the facility for processing. It was determined that the facility needed to process up to 60 m3h of diverse organic materials, including a variation of solids size up to 12 inches in diameter, ranging from potatoes to watermelons. It is important to have a consistent solids size for proper anaerobic digestion.
After initial grinding, which employs an M-Ovas® macerator followed by a TORNADO® T1-F Rotary Lobe Pump that conveys the material to the next part of the process, the system required mixing and conveying of dry matter between 13 to 20% and liquid manure substrate at total volume up to 80 m3h. The assumed viscosity of the mixture was 50,000 cPs and required discharge pressure up to 4 bar.
Compact and Reliable Solution
"After thorough consultations and meticulous planning with NETZSCH, we arrived at a solution that surpassed our expectations," stated the Customer. "NETZSCH worked closely with us, understanding our unique challenges, to design a system that not only fits into our very limited space but does so with fewer components than we initially believed possible. The elegantly simple and compact design is easy to access and maintain and offers consistent, reliable high performance, which is critical for our operations".
The system integrates the high-capacity N.Mac® Twin Shaft Grinder with infinite dry-running capability along with the NEMO® B.Max® Progressing Cavity Mixing Pump.
Grinders — The N.Mac® grinder is ideally suited to crushing and fragmenting the organic waste received by the customer, handling large and solid particles, whether wet or when the grinder operates dry.
The innovative FSIP® (Full Service-in-Place) design which was applied to the NEMO® B.Max® pump housing, allows for comprehensive maintenance of the robust Z-joint and cutting device replacement without the need to remove the entire grinder. This is a significant advantage given the challenges of performing maintenance in the cramped space where the system is located.
Mixing Pump — The NEMO® B.Max® pump complements the grinder by offering a design optimized for biogas applications, featuring a specialized feed hopper and feed/mixing screw for seamless product conveyance regardless of pressure and viscosity.
The pumping and mixing solution enabled the customer to control the solid content in the final product, ensuring the proper particle size and optimal mix between organic material and liquid substrate for the anaerobic digestion process. The ability to control the final product significantly enhances the operational reliability and efficiency of the downstream processes.
A Proven Excellence Fit
This compact and efficient solution not only has a small footprint, but it has also reduced the number of required tanks and eliminated the need for separate mixing units, thereby conserving space at the facility. The plant is been operating reliably and efficiently with less service times from past 2 years.