
18.02.2025
Choosing the Right Pump for Poultry Processing and Waste Applications
Positive displacement pumps provide optimal performance
In poultry processing operations, choosing the right pump is essential for efficiently handling the diverse demands of processing and conveying viscous products. Positive displacement (PD) pumps, including progressing cavity, rotary lobe, multi-screw, and peristaltic pumps, excel in these settings, particularly for food-safe conveyance in various processing steps or waste removal. Here’s an overview of how these pumps are applied and optimized in poultry processing, along with key selection tips to meet hygiene and operational needs.
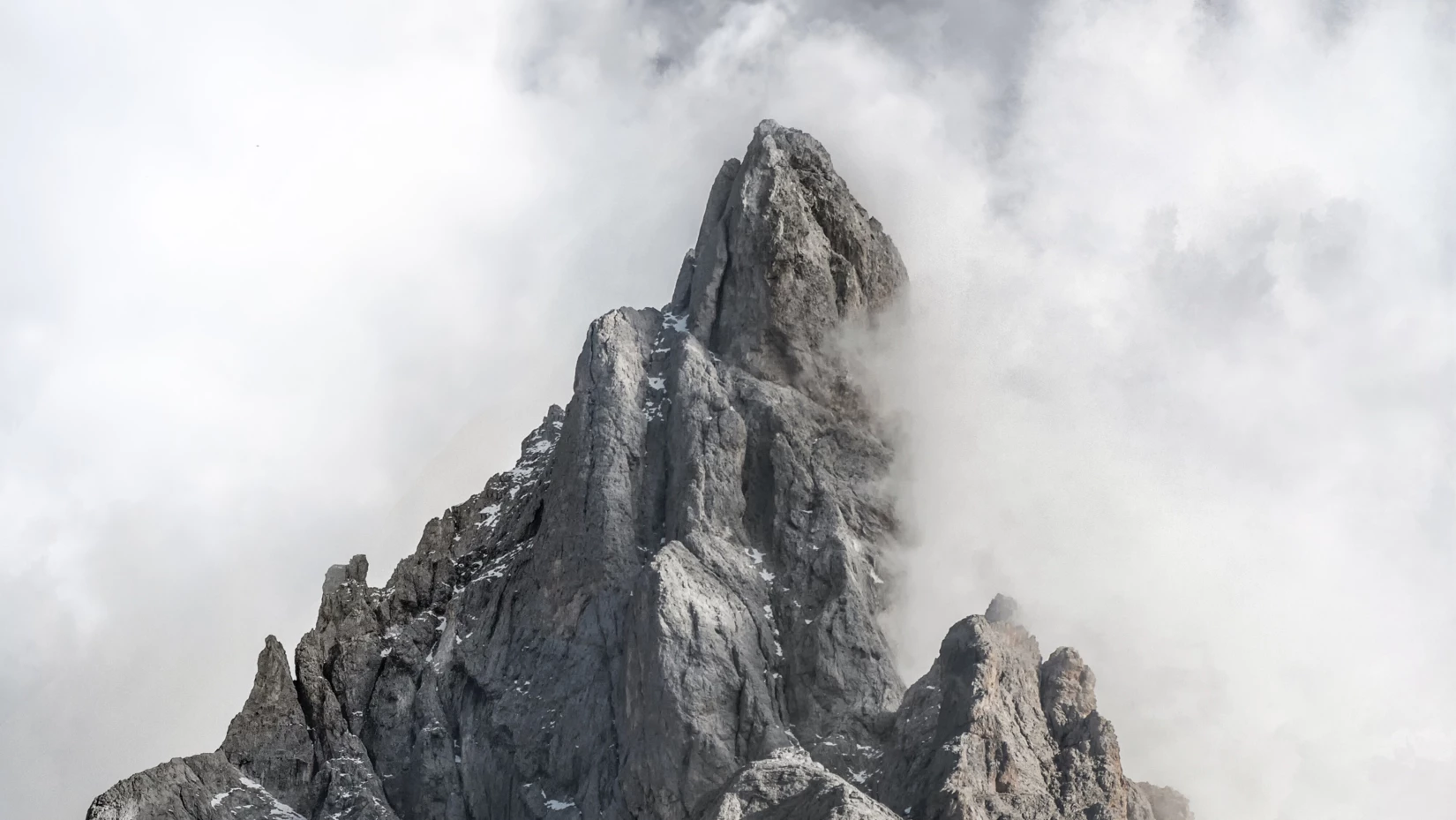
Customised Consulting
Role of Pumps in Poultry Processing
Pumps play a central role in poultry processing facilities. At the start of the operation, pumps are used to convey ground meat, deboned meat, trimmings, meat pieces, and chicken sausage, contributing to seamless processing. The process begins in the slaughterhouse, where whole birds are processed, cleaned, and eviscerated. Pumps then transfer these parts to further processing steps, such as cutting, packaging, or producing secondary products like chicken nuggets. Specialized pumps also handle sauces, fresh and used oils, and transport viscera to byproduct processing stages. Hygienic pumps facilitate the safe movement of meat products from one line to another, supporting high-speed production and streamlined processing.
At the waste-handling (back) end, pumps are critical in rendering waste, transferring organ meats, and conveying sludge from processing lines to wastewater treatment facilities. Here, PD pumps are valuable for dosing chemicals and metering wastewater, helping plants stay in compliance with environmental and sanitation standards.

New trend – x-ray in piping system
A new trend in poultry processing involves the use of pumps in conjunction with x-ray inspection systems embedded within piping. This setup is becoming a staple at the request of major retailers and food producers. X-ray systems help detect foreign materials like metal fragments or bone in meat products, which are then automatically removed from the processing line. Pumps are particularly suited to these systems, providing a steady, uninterrupted flow that facilitates quick identification and removal of contaminants, unlike traditional conveyor systems. This smooth flow allows operators to discard only small segments of product, minimizing waste.
Compliance and Cleanability Standards
Pumps used in poultry processing must meet rigorous food safety standards. For example, pumps should be FDA-compliant, ensuring that all materials used are safe for food contact and maintain structural integrity under processing conditions. Many operators also require pumps to be certified to the 3-A Sanitary Standards, indicating high cleanability and a reduced risk of contamination from microorganisms. Since most poultry plants undergo daily cleaning, equipment—including pumps—must support Clean-in-Place (CIP) procedures, which involve flushing with hot water, acid, and caustic solutions. PD pumps, like progressing cavity, rotary lobe, multi-screw, and peristaltic pumps, can integrate seamlessly into these CIP routines, contributing to both sanitation and efficiency.
Comparison of Pump Types for Poultry Applications
PD pumps are frequently the preferred choice in poultry processing due to their ability to handle viscous and particulate-laden products better than other pump types. Here’s a breakdown of common applications and suitable PD pumps:
Poultry Pump Applications and Recommendations | ||
Application | Pump type normally used | Alternative positive displacement pump recommendation and benefits |
Chicken trimmings | ● Low initial cost ● High maintenance cost over time ● Pressure limitations | Progressing cavity pump ● Can handle solids and gently convey product to long distances. ● Valve free pump |
Seasoning fluids metering | Gear pumps ● Commonly found in the market ● Mechanical seals used often fail and can be costly ● Noise is also a concern | Multiple screw pumps ● Mechanical seals that work on suction pressure and have much longer expected life ● Some can also serve as same pump for both process fluid and CIP process |
Offal and organ meats | Diaphragm pumps ● Low initial cost ● High maintenance cost over time ● Pressure limitations | Progressing cavity pump ● Can handle solids and gently convey product to long distances. ● Valve free pump |
Blood | ● Low cost pumps ● Shear the blood since they work on high speed | Peristaltic pump or rotary lobe ● Both types work with low speed and are much gentler to the fluid |
Cooking oils | Gear pumps ● Commonly found in the market ● Mechanical seals used often fail and can be costly Noise is also a concern | Multiple screw pumps ● Mechanical seals that work on suction pressure and have much longer expected life Some can also serve as same pump for both process fluid and CIP process |
X-ray inspection systems | Diaphragm pumps ● Low initial cost ● Generates pulsation in the discharge flow ● Pressure limitations | Progressing cavity pump ● Constant and non-pulsating flow. |
Waste food, Including DOA birds | Centrifugal pumps ● Low cost pumps ● Have limited capacity with solids ● Have issues with multiple operational points
| Progressing cavity pump ● Can handle high viscosity and presence of solids ● High pressure capability
|
Waste water | Centrifugal pumps ● Low cost pumps ● Have limited capacity with solids ● Have issues with multiple operational points
| Progressing cavity pump and Rotary lobe pump ● Can handle high viscosity and presence of solids ● Higher pressure capability
|
Real-World Examples of PD Pumps in Poultry Processing
NETZSCH has provided robust PD pumping solutions for numerous global poultry processors. Examples include:
- Trimmings Conveyance: A customer replaced their conveyor system with two NEMO® sanitary progressing cavity pumps, finding that the pumps more effectively handled low- to high-viscosity products with or without solids, improving both product integrity and operational efficiency.
- Ground Chicken for Sausage: A NEMO® pump with a rectangular inlet and feeding screw was chosen to convey ground chicken for sausage production, showcasing the pump’s capability to handle challenging, dense media.
- Internal Organs in Evisceration: In another plant, a NEMO® pump minimized maintenance demands in evisceration lines, proving resilient under continuous use.
- Sauces and Seasoning Conveyance: NETZSCH multi-screw pumps were selected for metering sauces and seasoning, offering shear-sensitive handling that preserved ingredients like spices, improving product quality and consistency.
Key Considerations When Selecting a Poultry Processing Pump
To ensure optimal performance and compliance, prioritize these factors when choosing a pump for poultry processing:
- Sanitary Standards Compliance: Seek pumps with 3-A Sanitary Standards certification for superior cleanability and FDA-compliance to meet food safety requirements.
- Low Maintenance Design: Choose pumps with fewer wear parts and robust construction to minimize maintenance and extend service intervals.
- Gentle, Low-Speed Operation: To maintain product integrity, look for pumps capable of handling high-viscosity fluids at low speeds, especially when high discharge pressures are required.
- Consolidated Supplier: Work with a supplier experienced in food processing who offers full technical support, parts, and after-sales services. NETZSCH provides these resources, along with in-house elastomer development and customization, ensuring the right pump fit for any application.
Ensuring the Right Fit: Collaboration with Experts
Selecting the ideal pump requires careful evaluation of the application’s specific requirements. By working closely with NETZSCH or another knowledgeable supplier, operators can ensure they get a pump precisely configured for their process, taking into account factors like operating temperature, flow rates, suction requirements, discharge pressures, and solid content. This attention to detail guarantees that the pump will perform reliably and meet the demands of the poultry processing environment.