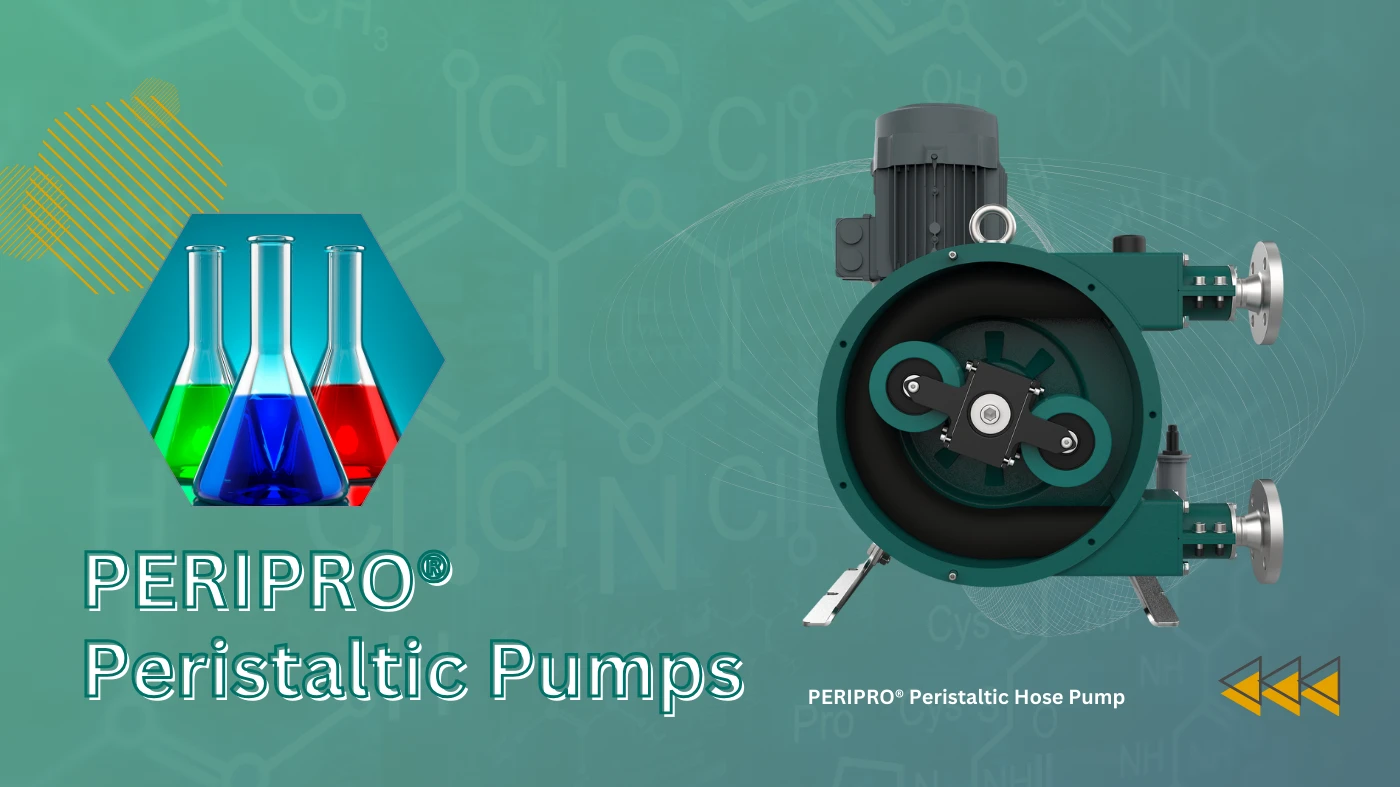
18.02.2025
Unlocking Efficiency: The Advantages of Peristaltic Pumps
Peristaltic pumps have emerged as a revolutionary solution in industrial pumping, offering a myriad of benefits over traditional pump technologies. By leveraging a flexible, compressible hose, these pumps offer unmatched durability, efficiency, and versatility, addressing the challenges faced by conventional pump technologies. Here’s a look at how peristaltic pumps are reshaping industries from wastewater treatment to chemical processing, delivering exceptional performance and cost savings.
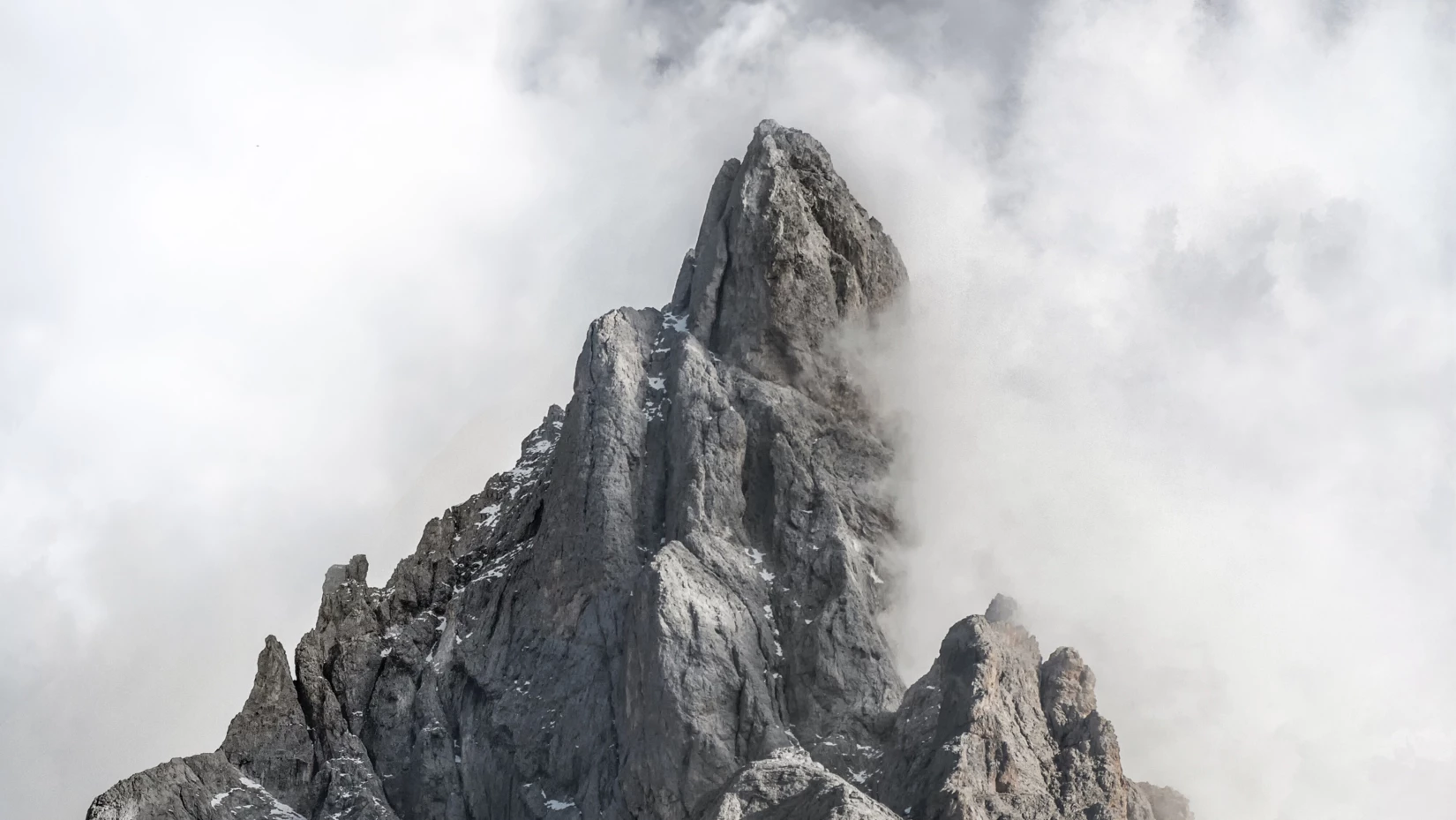
Customised Consulting

Harnessing Peristalsis
Peristaltic pumps operate on the principle of peristalsis—similar to how the human body moves food through the digestive system. A roller or shoe compresses a flexible hose in a sequential motion, creating a vacuum that draws fluid in and propels it forward. This continuous compression and relaxation action enables precise, controlled flow while isolating the fluid within the hose, minimizing contact with pump components. This design ensures several key advantages, especially in applications where product integrity, wear resistance, and low maintenance are essential.
Peristaltic pumps are known for their gentle pumping action, making them ideal for handling shear-sensitive fluids and delicate media. This feature ensures that product integrity is maintained, making them a popular choice in industries such as wastewater treatment, chemical, paper & pulp, food and mineral processing.
For example, in the wastewater treatment industry, precise metering and conveyance of chemicals, flocculants and reagents are critical for ensuring efficient treatment and reliable operation. Peristaltic pumps excel in this regard, providing accurate and reliable pumping with low and easy maintenance. Similarly, in the food processing industry, where maintaining the texture and quality of products such as fruit preserves, sauces, and confectionery is paramount, peristaltic pumps offer an ideal solution. Their gentle pumping action minimizes shear forces, ensuring that delicate ingredients are handled with care. This not only improves product quality but also reduces waste and increases yield, leading to significant cost savings for manufacturers. In the mineral processing industry, often the mineral product slurries cannot be crushed, ground-up or damaged in any way after they have been produced.
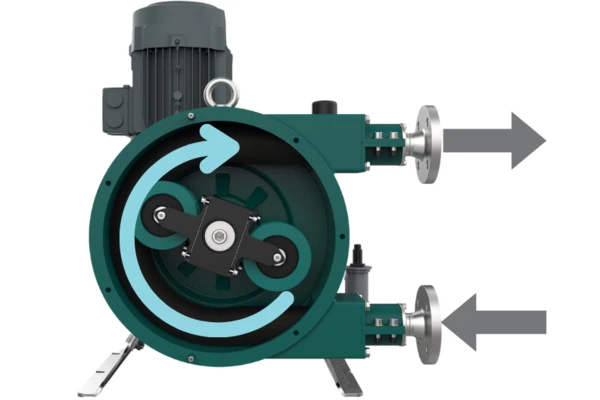
Advantages of peristaltic pumps
One of the most significant advantages of peristaltic pumps is the hose is resistant to high abrasion. The design of these pumps ensures no contact between the pumped fluid and the pump components, except the hose, reducing wear and tear on the pump components and the high-quality hose with a unique manufacturing process: extruded inner layer with high-density textile reinforcement and precisely machined outer layer ensures optimal compression and withstands wear and tear.
This advanced manufacturing technology extends the life of both the pump and the hose. For industries handling abrasive materials such as mining, wastewater treatment, and lately the emerging lithium-ion battery recycling industry, the hose durability is crucial for maintaining consistent and reliable operation. Traditional pump technologies often suffer from rapid wear of the multiple wetted parts and require frequent maintenance and replacement of components. However, peristaltic pumps with advanced hose designs can withstand the harshest operating conditions, resulting in reduced downtime and lower maintenance costs. For example, in mining applications where pumps are exposed to highly abrasive slurries, peristaltic pumps with abrasion-resistant hoses can significantly extend service intervals, reducing the need for frequent maintenance and parts replacement. Similarly, in wastewater treatment plants, where pumps are required to handle corrosive chemicals and abrasive solids, peristaltic pumps offer unmatched reliability and durability. By minimizing wear and tear on pump components, these pumps help operators reduce maintenance costs and increase overall efficiency.
Peristaltic pumps are also incredibly versatile, and capable of handling a wide range of fluids, including corrosive chemicals, viscous slurries, and abrasive materials. This versatility makes them well-suited for use in various industries. For example, in chemical processing plants, where a broad assortment of corrosive chemicals are used in manufacturing processes, peristaltic pumps offer an ideal solution. Their seal-free design and compatibility with a variety of elastomers make them suitable for handling even the most aggressive chemicals, ensuring reliable and efficient operation. Similarly, in wastewater treatment plants, where pumps are required to handle abrasive slurries and corrosive chemicals, peristaltic pumps provide unmatched versatility and reliability. Their ability to handle a variety of fluids with ease makes them an indispensable tool for operators looking to maximize efficiency and minimize downtime. Whether pumping corrosive acids, viscous slurries, or abrasive materials, peristaltic pumps deliver consistent and reliable performance, ensuring smooth operation in even the most challenging environments.
Another key advantage of peristaltic pumps is their dry running capability. Unlike many traditional pump technologies, peristaltic pumps can run dry indefinitely without risk of damage. This reliability reduces the need for complex monitoring systems, making them a cost-effective and low-maintenance option. For industries where downtime is not an option, this dry running capability is invaluable. Their ability to run dry indefinitely ensures uninterrupted operation, even in the event of unexpected shutdowns or process interruptions such as a closed valve or a low supply tank level.
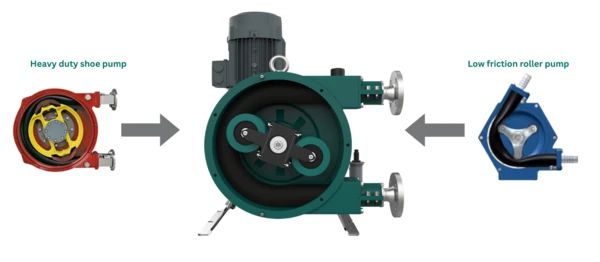
With only one wear part, the hose, peristaltic pumps are easy to maintain and repair. Routine maintenance tasks can be performed quickly and easily by onsite personnel, eliminating the need for specialized technicians which reduces downtime. This simplicity and ease of maintenance make peristaltic pumps an attractive option for many industries. By eliminating the need for specialized technicians and reducing downtime, these pumps help operators maximize efficiency and minimize operating costs. Whether pumping corrosive chemicals, abrasive slurries, or viscous fluids, peristaltic pumps deliver consistent and reliable performance, ensuring smooth operation in even the most demanding applications.
Case Study: Peristaltic Pump Sodium Hypochlorite Service Success
Sodium hypochlorite (NaOCl) is widely used by municipal water treatment plants as an effective water disinfectant. However, traditional dosing pumps, such as Electrically Operated Double Diaphragm (EODD) pumps, are prone to vapor locking when gas bubbles build up in the feed system, leading to frequent manual venting and high maintenance costs.
To address these issues, PERIPRO® peristaltic pump was specified for sodium hypochlorite dosing services. Its ability to run dry indefinitely, pump harsh chemicals, and accurately meter product flow has eliminated vapor locking problems, saving water utilities thousands of dollars per pump, per year.
The PERIPRO® requires minimal maintenance, with only the elastomer hose needing replacement when necessary. After a year of continuous operation, the initial pumps are still performing well, demonstrating their reliability and cost-effectiveness.
Peristaltic Pumps: Innovative Design Offers Durability, Versatility, and Reliability
NETZSCH PERIPRO® peristaltic hose pumps offer several additional advantages over traditional peristaltic pump designs. With an innovative large roller design and a choice of four elastomers, including EPDM, Natural Rubber, NBR, and Hypalon, these pumps are suitable for various industrial applications. They are engineered for durability, with heavy-duty rollers and oversized shaft bearings that are designed to withstand the rigors of 24/7 operation and not require maintenance or replacement. A seal-free design eliminates the risk of seal failure, removing the chance of hazardous or volatile chemicals being released because of a failed seal.
These pumps can handle up to 70% solids, making them ideal for pumping slurries and other high-solid content fluids. With their compact design, NETZSCH peristaltic pumps are desirable for applications where space is limited, allowing for easy installation in tight spaces.
Peristaltic pumps have numerous advantages over traditional pump technologies. With their gentle pumping action, high durability, and versatile performance, they are the ideal choice for a wide range of industrial applications. Whether you need to pump corrosive chemicals, abrasive slurries, or shear-sensitive fluids, peristaltic pumps deliver reliable performance and peace of mind.