NEMO® Multiphase progressing cavity pumps are an efficient pumping solution for conveying multiphase fluids, that are mixtures of oil, gas, and water. These mixtures can be high gas or with high solids from the oil production wells. These multiphase liquids are to be transferred to gathering stations for further processing.
Multiphase pumps keep oil and gas production viable, even with increased gas, water or sand content coming out of Oil wells. The progressing cavity multiphase pumping principle eliminates the need for space consuming separation devices, separate pumps, compressors, and lines at the well. This allows for continuous and efficient pumping without initial phase separation.
The NEMO Multiphase pumps help conserve natural resources and protect the environment. The closed system with minimal leakage points prevents flaring in fields. High standards for equipment and safety are crucial in oil fields. NEMO® pumps significantly contribute to this safety and reliability. They handle a range of media complexities, from high to low viscosity and from shear-sensitive to heavily loaded with solids.
The innovative design of NEMO® Multiphase progressing cavity pumps enables efficient process control. These pumps comply with the API 676 3rd Edition standard and NACE MR-01-75 requirements, ensuring safe, reliable pumping with maximum efficiency.
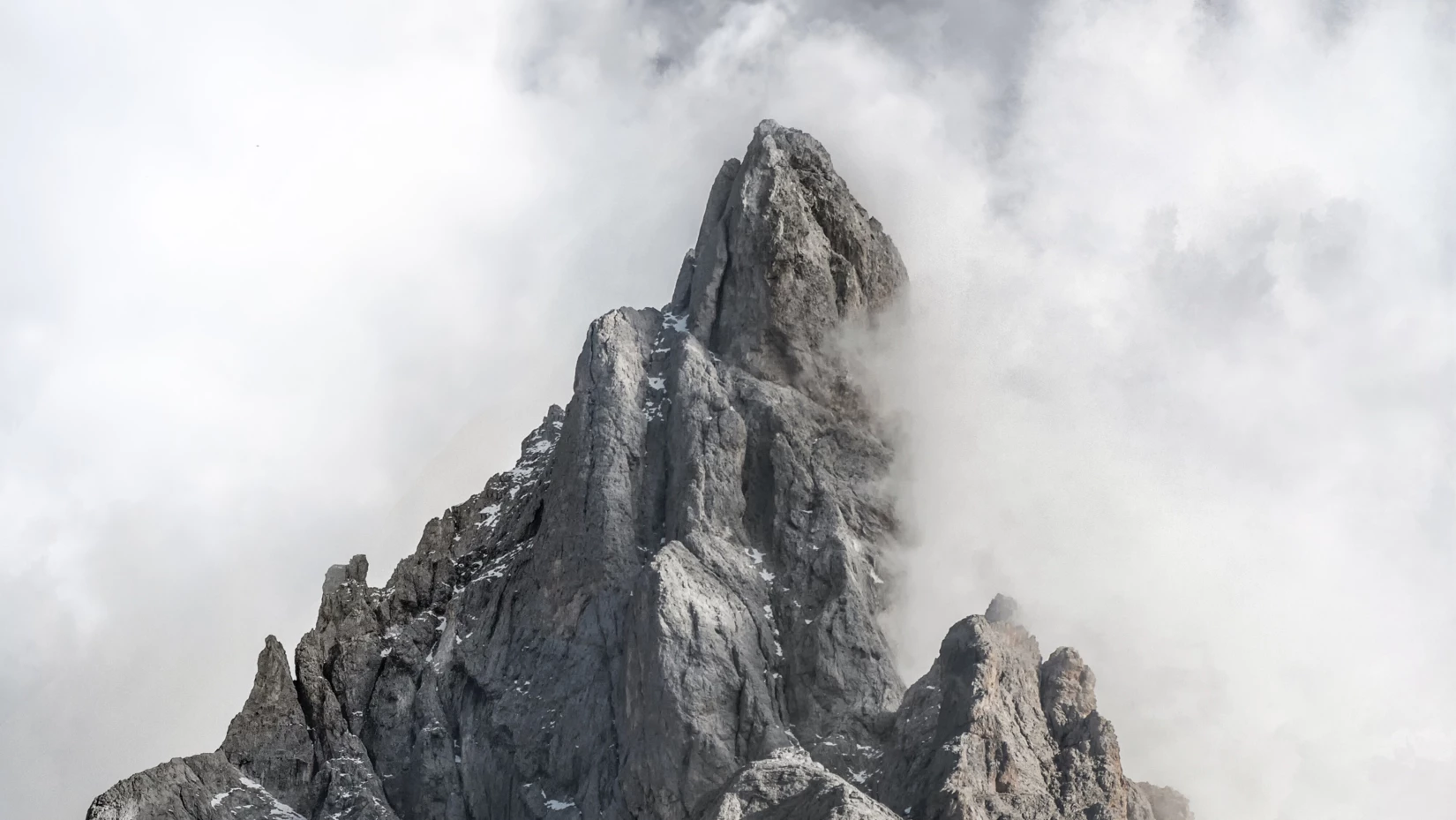
Individual Consulting
Multiphase Pump Advantages
Efficient handling of Multiphase liquids in Oil Fields
Constant flow under varying pressures
Highest Safety
NEMO® Multiphase Progressing Cavity Pump Construction
The NEMO® Multiphase Pump is designed to handle the challenges of multiphase fluids under different pressures and temperatures in oil and gas production. Its robust and efficient design ensures reliable performance and easy maintenance, making it ideal for tough environments.
The key components are a rotating Rotorrotor,Rotors,rotorsrotor and a static stator. As the rotor turns within the stator, cavities form between the stator and the eccentrically rotating rotor. These cavities progress continuously in rotating motion along an axial direction. The volume of fluid in each cavity stays constant and moves smoothly, so there’s no shearing, squeezing, or pulsating effect on the fluid during transfer. As the rotor is inserted into the stator it creates sequential cavities. When the rotor is rotating inside the stator these cavities, are moved axially, alternating the opening and closing of each one, progressively and uninterruptedly from the suction to discharge, causing the pumping action. In other words, one cavity reduces volumetrically and another one increases at the same proportion from suction to discharge leading to a continuous and non-pulsating displacement flow.
In elastomer stator designs, pumping occurs through the compression fit between the rotor and stator, creating a physical contact line along the length of the rotor. This is obtained by designing the rotor diameter (dr) slightly greater than the inside diameter of the stator (ds). The pumped liquid lubricates and cool the compressed rubbing surfaces of the rotor and stator.
For liquid applications, the compression between the rotor and stator needs to be relatively tight to ensure the pump operates with optimal volumetric efficiency. The compression fit must not be high or the mechanical load on the rubber can become too much and the rubber material can tear. The compression fit becomes critical when the pump works in multiphase applications. It's important to strike a balance between achieving good volumetric efficiency and avoiding excessive compression, which can lead to frictional heat during periods of gas slugging.
Higher viscosity crude oils have a positive influence on the pumps volumetric efficiency. Proper system integration is crucial to handle process challenges like prolonged slugging. More than in any other application for progressive cavity pumps, the system must be designed to work in harmony with the pumps, ensuring they aren’t damaged during such events. A simple liquid collection tube and recycle line arrangement is a reliable way of metering the flow back into the multiphase pump. Most often actually applied with recycle line flow controlled by a throttle valve which is set manually. The leakage collection device is sized to provide a buffer of fluid, allowing for a reasonable operating period that aligns with the typical slug flow duration based on the field operator's experience.
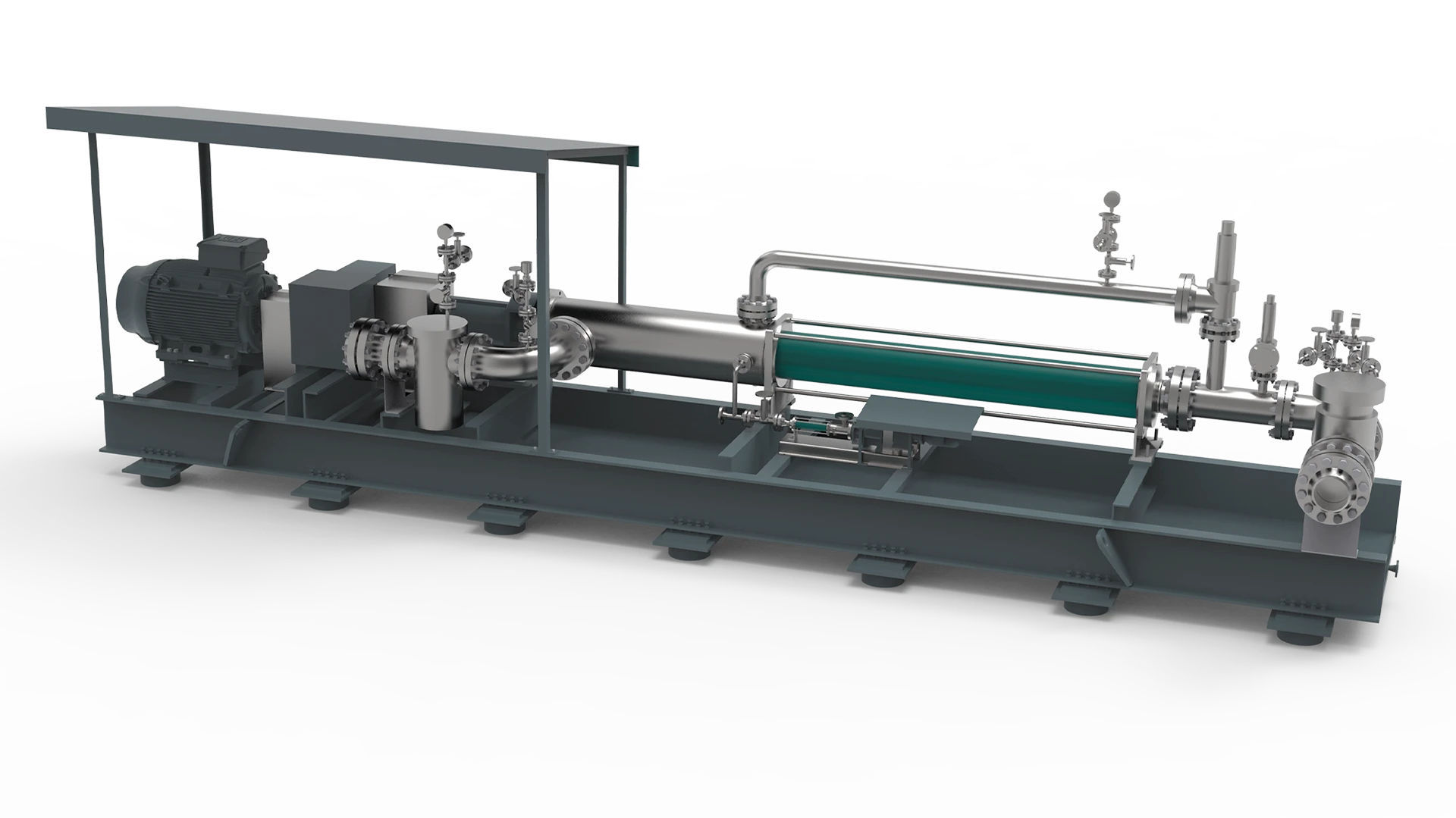

Comprehensive Service and Support
At NETZSCH, our commitment to your success extends well beyond the initial purchase of your NEMO® BO/BS Progressing Cavity Pump. We offer a complete range of aftermarket services to ensure your pump operates at peak efficiency and reliability throughout its lifecycle.
- Consultation: Our experts provide tailored advice to help you select the right pump configuration and optimize your processes.
- Spare Parts: We maintain a full inventory of genuine spare parts to minimize downtime and ensure optimal pump performance.
- Maintenance: Our routine and preventative services keep your pump running smoothly and prevent unexpected breakdowns.
- Repair: Swift and Efficient: Our prompt repair services ensure minimal disruption and a quick return to operation.
- Modernization: We offer modernization services to keep your pump system up to date with the latest technology and performance standards.
Your contacts and companies at NETZSCH
Any specific questions? Contact us for help or fill in the contact form.