
31.10.2024
About Progressing Cavity Pumps from the World Market Leader – NETZSCH Pumps & Systems
NETZSCH Pumps & Systems, the world market leader in the field of progressing cavity pumps, has the answers to your questions.
With more than 70 years of expertise in engineering, designing, manufacturing, supplying, and servicing progressing cavity pumps worldwide, NETZSCH Pumps & Systems is publishing insights about progressing cavity pumps. Everything you need to know about this proven technology can be found here.
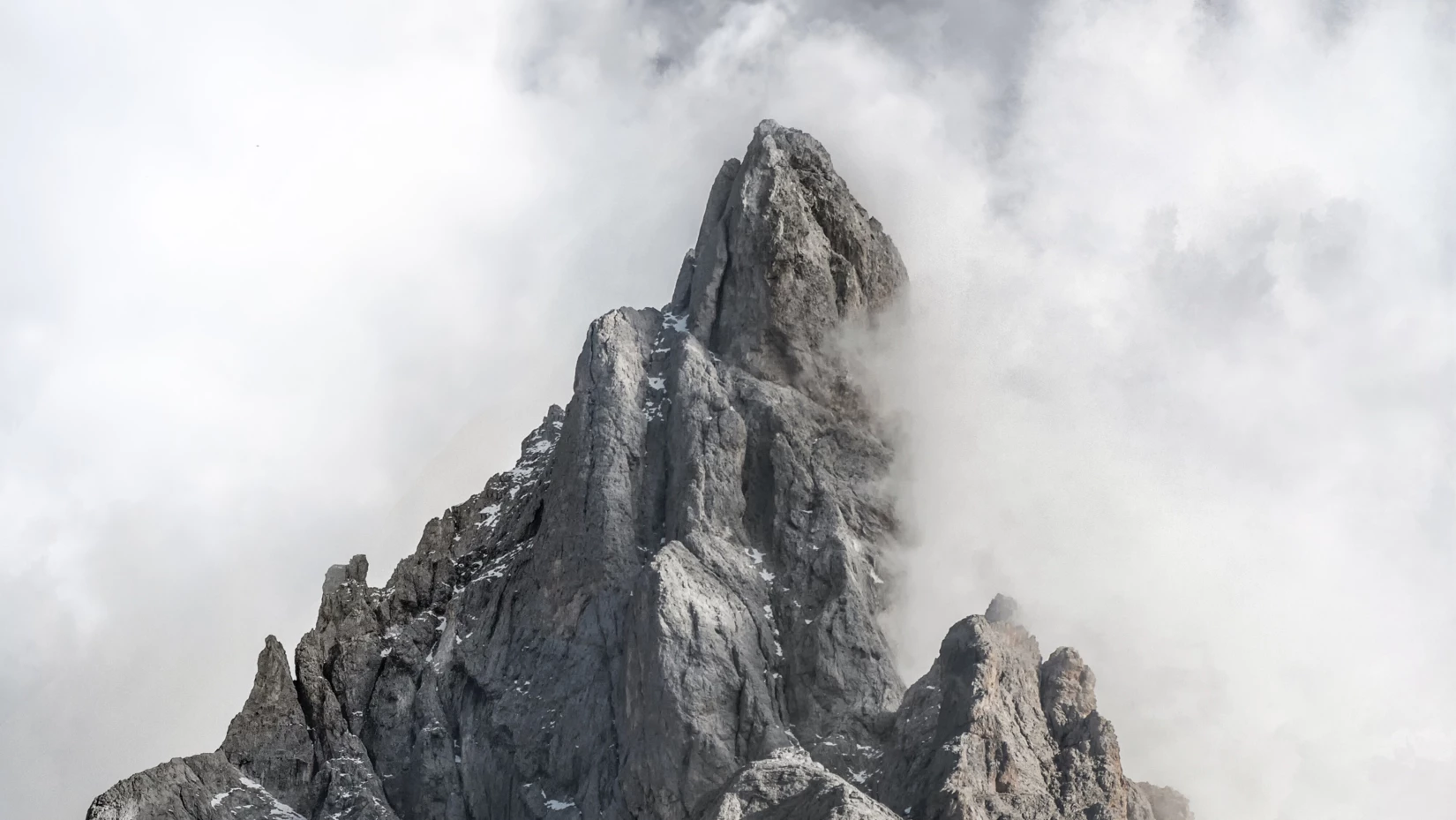
Customised Consulting
Construction of Progressing Cavity Pumps
Progressing cavity pumps (also known as eccentric screw pumps or single screw pumps) are from the family of Rotary Positive Displacement pumps that consist of are built around two key components, the pumping elements, each contributing to their unique ability to handle a wide range of fluids, from low to high viscosity, abrasiveness, aggressiveness and even those containing solids. Inferring to the technology inventor, Prof. René Moineau, they are also known by other names which are derivates of his name, Mohno pumps, among others. The main components of progressive cavity pumps are:
- Rotor
- Stator
- Pump housing ( Suction) and End Flange ( Discharge)
- Coupling rod and the Drive Train
- Shafe Seals
- Drive shaft
- Drive unit

The Rotorrotor,Rotors,rotorsRotor and the stator which are the core pumping elements are the heart of a progressing cavity pump. The Rotorrotor,Rotors,rotorsrotor is a helical-shaped screw that rotates within the stator. As the rotor turns inside the stator, it forms sealed cavities with the stator. These cavities at the suction end create a vacuum enabling the suction of the conveying fluid into the pumping elements. They progress along the length of the rotor and stator, moving the fluid from the pump’s inlet to its outlet.
The stator is an internally helical component that complements the rotor’s shape but has an additional pitch, creating the progressive cavity. The properties of the elastomer-stator are critical to maintaining precise sealing, ensuring smooth and efficient fluid transfer, and preventing backflow referred to as slip.
The coupling rod and the drive train along with the drive shaft connect the Geared Motor drive to the rotor. It transmits the torque to the rotor while allowing for the rotor to accommodate an eccentric motion as it rotates. The drive train design with minimum eccentricity and robust joints to accommodate the eccentric motion is critical for the long service life of these rotary units.
Shaft Seals are crucial in maintaining the integrity of the pump and the fluid, preventing leaks, and protecting the environment. The shaft seal is mounted on the drive shaft and secured on the flow path of the fluid ensuring the lowest amount of dead space for the fluid or its solids to accumulate. Several shaft seal options such as self-lubricated gland packing, lip seals, and single and double-acting seals of various designs, supported by relevant seal plans can be easily accommodated to ensure smooth and safe operation.
The Pump housing encloses the drive train and has the suction connections for the fluid inlet and during reversible operation serves as the outlet. The pump housing also serves well as a buffer fluid chamber when the pump needs a prime at negative lift operations. The end stud serves as the discharge port on the pressure side and based on the direction of rotation can be used as a suction port as well. The housing and end port designs can be adapted based on industry needs. Food grade applications can be provided, suited polished surfaces for easy cleaning, and also relevant connections such as SMS unions are similar. These parts can also be provided in various materials based on the corrosive nature of the fluids, providing for sufficient corrosion allowance based on NACE standards.
The prime mover of this type of pump is the drive unit that moves the rotor. This can be an electric motor, a hydraulic motor or other drive mechanisms such as diesel engines directly mounted. These pumps commonly operate in a speed range from 80 -600 rpm to suite the flow property of the viscous fluids they commonly convey.
Function of Progressing Cavity Pumps
The progressing cavity pumps work on the positive displacement principle, where the fluid is drawn into the pump by virtue of the vacuum created at the suction end of the pump, and thereafter displaced to the discharge end by virtue of the Rotary motion of the pumping element.
The eccentrically rotating rotor forms a cavity within an elastic stator which is an elastomer that moves fluid from the pump’s inlet to its outlet. This rotary positive displacement action ensures a consistent flow, regardless of pressure changes or fluid viscosity, over a wide range.
This makes this technology ideal for applications that require precise and reliable fluid transfer. The pump’s helical design allows it to handle thick, viscous fluids and those containing solids without damaging them, which is crucial for applications involving shear-sensitive or high-viscosity materials. The pump provides a continuous, non-pulsating flow, essential for processes requiring minimal fluctuations.
Progressing cavity pumps have excellent self-priming capabilities, enabling them to draw fluid into the pump under vacuum conditions or for negative lift operations. The versatility of these pumps extends to various fluid types and conditions, including abrasive, corrosive, or temperature-sensitive fluids, making them suitable for industries such as food and beverage, oil and gas, chemical processing, and wastewater treatment.
Furthermore, their gentle, non-turbulent pumping action minimizes shear and agitation, making them ideal for delicate or shear-sensitive materials. Overall, progressing cavity pumps are valued for their reliable, precise, and adaptable fluid handling solutions across demanding applications.
Advantages of Progressing Cavity Pumps
- Progressing cavity pumps can handle fluids with wide ranges of viscosities from 1 Cps to 3 Mill Cps, high and low abrasiveness, and solids, shear sensitive and corrosive They are capable of pumping everything from thin liquids to thick, viscous slurries, making them suitable for diverse applications
- Progressing cavity pumps are capable of effectively managing fluids containing solids or particulates, making them suitable for industries like mining, wastewater treatment, and chemical processing where such materials are common.
- These pumps provide a continuous, non-pulsating flow, which ensures steady and reliable fluid flow. This consistent flow is essential for processes that require precise control and minimal fluctuations. The enables excellent and precise flow control.
- The design of progressing cavity pumps ensures gentle, non-turbulent fluid movement, which reduces shear and agitation. This makes them ideal for handling delicate or shear-sensitive materials, such as those found in the food, pharmaceutical, and cosmetic industries.
- Progressing cavity pumps are self-priming, allowing them to draw fluid into the pump at very low suction pressure conditions such as negative lifts. This feature is particularly beneficial when dealing with fluids under vacuum.
- Due to their robust construction and simple design, progressing cavity pumps generally require less maintenance compared to other pump types. This reduces downtime and operational costs.
- Built with high-quality materials and designed to withstand demanding conditions, these pumps offer a long service life, even in harsh environments. This durability contributes to their overall cost-effectiveness.
Heating
FSIP® Design
Versatility
Limitations of Progressing Cavity Pumps
Despite their advantages, progressing cavity pumps also have some limitations.
- The interference fit in the pump elements will require a minimum of lubrication for smooth and continuous operations. Hence they can be sensitive to dry running if not sufficiently lubricated, leading to increased wear.
- The pump core pumping element has a metal rotor and a stator which is an elastomer. The construction of the elastomer limits the pump in its ability to handle fluids above 160 degrees C.
- The progressive cavity pump is a long pump in physical dimensions which can be a constraint in some installations against technologies that can handle similar applications.
Areas of application for progressing cavity pumps
Progressing cavity pumps are used in various industries due to their versatile and customizable design options.
In food processing, for example, they are suitable for gently transferring viscous substances such as sauces, doughs or creams.
The progressing cavity pumps enable the gentle transfer of abrasive and aggressive media in the chemical industry. This reduces your maintenance and repair costs in the long term. In wastewater treatment, progressing cavity pumps are used for pumping sludge and sewage sludge, as they can also move solid components.
Progressing cavity pumps also offer a sustainable solution in the oil and gas industry, for example, for transferring drilling mud. In paper production and mining, where they efficiently pump a wide range of media with varying consistencies. Therefore, the application areas for progressing cavity pumps extend across various industries where precise, gentle and reliable pumping of different media is required.
Progressing cavity pumps from NETZSCH
As a global specialist in conveying complex media, NETZSCH's portfolio includes rotary lobe pumps, multi-screwpumps, peristaltic pumps, grinding systems, and barrel emptying systems as well as progressing cavity pumps.
Thanks to numerous models, we cater to various applications in a wide range of process industries. Whether environment & energy, chemical, pulp & paper, food & pharmaceuticals, mining, oil & gas upstream, mid- / downstream, or batteries: We develop a customized and sophisticated progressing cavity pump solution for your inquiry.
Brochure