SUSPENSIONS
Efficient Pumping of Abrasive and Non-Abrasive Suspensions
How Honeywell sustainably reduced plant downtime and maintenance costs
The more different suspensions and other liquids are pumped, the greater the challenges for the pumps. Honeywell Specialty Chemicals GmbH, based in Seelze in Lower Saxony, also struggled with severe wear and tear and costly plant shutdowns.
The problems were caused by highly abrasive suspensions and rinsing cycles with deionised water. We show you how the chemical producer, together with NETZSCH Pumps & Systems, reduced production losses when pumping suspensions and ensured its high-quality standards.
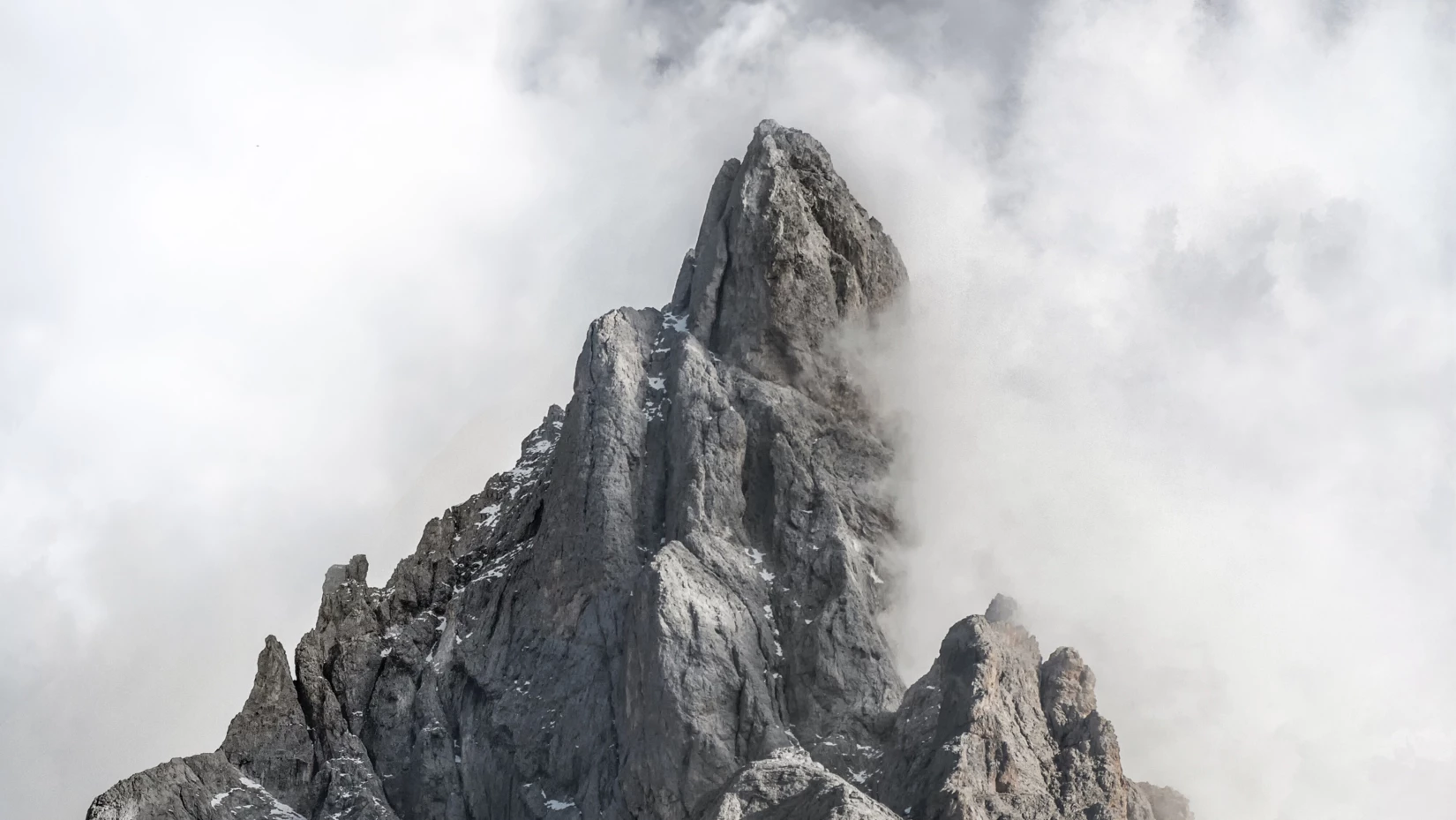
Individual Consulting
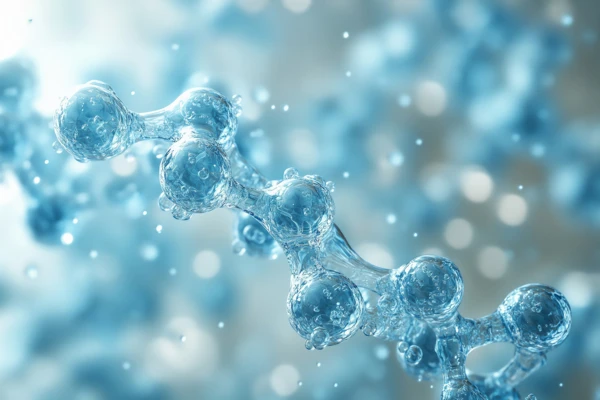
Downtime when pumping suspensions despite redundant operation
Honeywell's suspensions are used for demanding applications in electronics, pharmaceuticals and research, as well as in other industries such as automotive, construction and textiles. More than 500 different suspensions are produced at the German site in Seelze. This wide variety of suspensions poses several challenges, particularly for the pumps used. Despite the redundant operation, two older progressing cavity pumps, which had been used by the company for more than 40 years to pump suspensions and liquids, some of which were highly abrasive, were increasingly causing plant shutdowns. The system was cleaned between product runs with demineralised water, which is particularly aggressive towards metallic surfaces. Alternating cycles with abrasive and non-abrasive media, as well as the intermediate rinsing cycles, made it challenging to design the materials of the stator and the other pump components for the respective media. Despite frequent refitting, it was almost impossible to prevent wear. To reduce downtime, the two aggregates ran in redundancy operation. The highly abrasive properties of the suspension meant the pump's stator wore remarkably quickly and had to be replaced not only after the product cycle of usually four weeks but, in some cases, up to twice a day. These unplanned downtime and production losses resulted in high costs.
Pumping suspensions: Process optimisation with NETZSCH
As a global specialist in customised pump solutions with more than seven decades of experience, we at NETZSCH not only develop, produce and distribute a wide range of pumping technology for complex applications but also support you in all matters relating to design, maintenance and modernisation. To make production at Honeywell Seelze more resilient and to optimise internal processes given the demanding range of pumped media, a solution could pump all the suspensions used in the plant without needing prior adjustment. The aim was to significantly reduce wear on the pumps, even with highly abrasive suspensions, and to be able to replace the affected components quickly and easily. In close cooperation with Honeywell and NETZSCH, a sustainable solution for pumping the suspensions was found.
How Honeywell pumps suspensions with maximum efficiency
“Based on these requirements, we recommended a TORNADO® T.Proc® rotary lobe pump in an all-metal design”, explains Christian Eckert, Area Sales Manager at NETZSCH. “The modern rotary lobe pump is particularly wear-resistant and easy to maintain.” This is due to the innovative FSIP® (Full-Service-in-Place) design, which enables complete cleaning with CIP and SIP and allows direct access to the pump chamber, avoiding time-consuming dismantling for service and repair work. At a pressure of 3.5 bar, the TORNADO® T.Proc® at Honeywell Seelze pumps around 2.0 m3/h of suspensions containing up to 32% solids. For most suspensions and liquids, as well as for the deionised water, pistons made of stainless steel CrNiMo17-12-2 were selected, which is characterised by high corrosion resistance and strength. Only highly abrasive media could not withstand them for long. Unique tungsten carbide-coated pistons are now used to pump these suspensions reliably and survive a four-week production campaign.
While integrating the pump into the production process for suspensions, the pump was initially opened several times and serviced as a precaution. Thanks to the FSIP® design, Honeywell employees quickly gained routine in maintenance work and could carry it out without lengthy interruptions to production. The spatial separation of the pump and gearbox chambers ensures maximum operational reliability even during maintenance. “The TORNADO® T.Proc® runs smoothly - regardless of the product being pumped. This saves time-consuming conversions and repairs. The old pump had to be converted every time the product was changed. This is now a thing of the past”, says Eckert.
TORNADO® T.Proc® rotary lobe pump
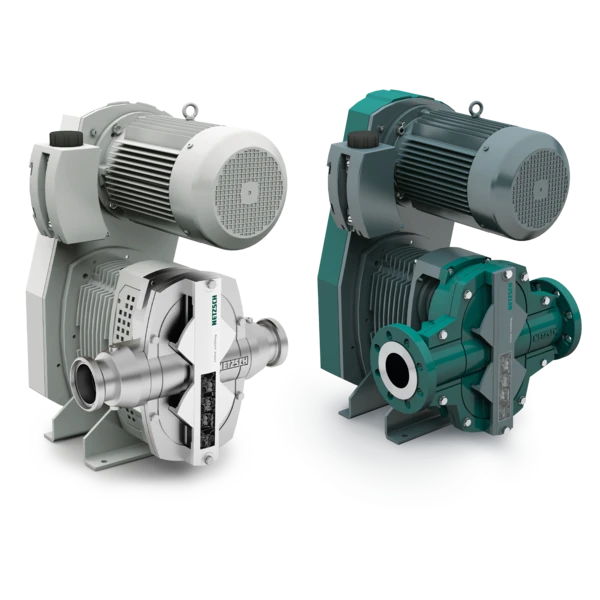