HYDROGEL
Customised Pump Solution Optimises Hydrogel Production in Chemical Plant
How NETZSCH ensured an efficient homogenisation of hydrogel lumps
Quality and efficiency – precision in handling fluids is crucial to ensuring both in the chemical industry. This was also the case for a traditional German chemical plant facing particular challenges in homogenising lumps of hydrogel.
The goal was to produce a homogeneous flow of uniform particle size. Considering the medium's sensitivity, this challenging task required an individual pump solution. By working with NETZSCH Pumps & Systems, the global specialist in handling complex media, the manufacturing process was optimised in terms of quality, time, and costs. Today, the chemical plant benefits from a highly flexible production process, offering a wide range of hydrogels.
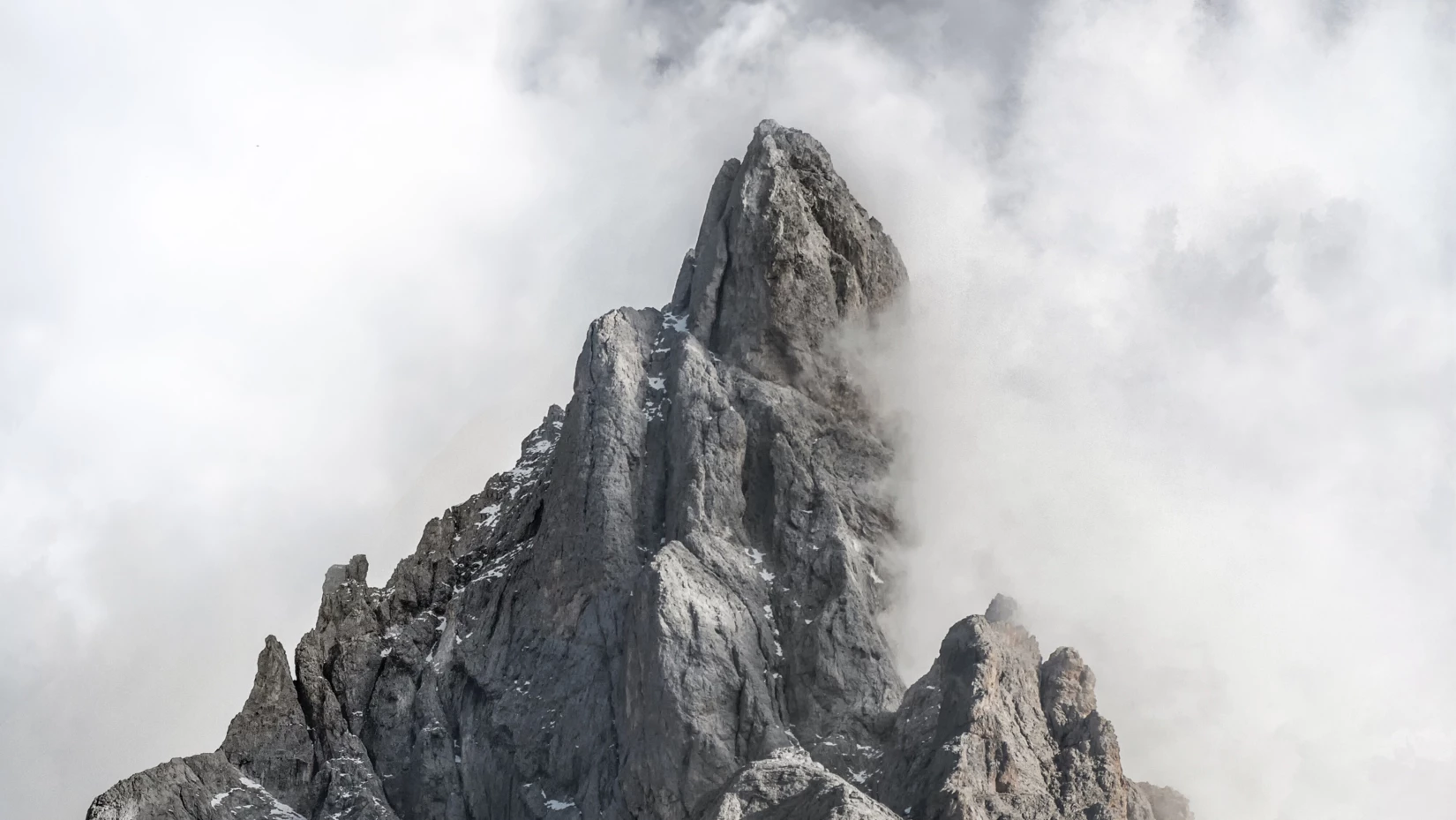
Individual Consulting

Efficient homogenisation: From hydrogel to versatile silica gel
As an expert in producing inorganic speciality chemicals, the company manufactures high-quality materials for users in various industries, including hydrogel. This is used to produce silica gel, typically utilised in the protein stabilisation of beer, as a matting agent in paints and varnishes, or as a coating for inkjet paper. Therefore, up to 30 millimetres of hydrogel lumps must be homogenised to produce a uniform flow rate with a consistent particle size. Of course, as always in the chemical industry, efficiency and product quality are top priorities in this process.
Fine line between optimal results and destruction of the hydrogel
The material must be treated precisely and gently to achieve the desired particle size without damaging the product. Due to the hydrogel's shear sensitivity, the manufacturing process is subject to conflicting priorities: On the one hand, the product should be optimally processed, but on the other hand, shear forces can destroy it. To balance these conflicting priorities, the shear rate must be controlled, and homogenisation must be monitored. Only using the appropriate technology can even and uniform particle sizes essential for the downstream decanter process be achieved. At the chemical plant, homogenisation of the hydrogel was initially based on an energy-intensive thermal drying method. In addition to the high operating costs, this led to unsatisfactory particle consistency and quality results.
Highest efficiency and flexibility in homogenising hydrogel
Together with the experts from NETZSCH, an innovative pump system optimally tailored to the requirements of homogenising hydrogel was developed. As a global specialist in handling complex media and with more than seven decades of experience, NETZSCH offers sophisticated, customised pump solutions for every application. This also includes testing solutions and, if necessary, adapting them until they are optimally suited for the specific application. “We really appreciate the fact that we had the opportunity to test the system in advance. This was a deciding factor for us when selecting the supplier”, reports a project manager from the chemical plant. Thanks to all stakeholders' short communication paths and quick reaction times, developing a suitable approach took only three months. The result was a system combining two types of positive displacement pumps: the NEMO® progressing cavity pump and a specially adapted TORNADO® rotary lobe pump. The NEMO® pump draws the hydrogel out of the storage containers, ensures a continuous flow and conveys the medium to the TORNADO®. Here, homogenisation is done by two counter-rotating circular rotors, which grind the medium. The rotors are set to a defined gap and thus largely determine the particle size. Afterwards, the hydrogel is dried in a chamber filter press. The unique feature of this combination is that the TORNADO® has been optimised for this application. It acts as a shearing unit and grinder - this is where the actual homogenisation of the hydrogel takes place. Special toothed pistons with a machined surface and adapted gap spacing ensure the lowest possible pressure losses.
The synergy between the upstream NEMO® Pump and the TORNADO® ensures an optimised process, guaranteeing uniform particle size and consistent conveyance of the shear-sensitive medium. All materials and technologies used ensure a high level of chemical resistance. CIP and SIP processes have been considered, dead spaces have been eliminated, and food-compliant surface quality and finish are guaranteed. But that's not all: Using the new technology, the chemical company can adjust the machine's operation depending on the product's properties. Both the direction of rotation and the speed can be selected manually – providing an entirely new control and flexibility in process management. This opens up additional possibilities in the product portfolio because the entire range of silica gels with different product properties can be covered. Using two NETZSCH pumps has proven to be a win-win situation for the medium-sized family business. “The throughput and quality meet our expectations, and we were also impressed by the support and advice we received from NETZSCH”, says the project manager happily.
NEMO® BY progressing cavity pump und TORNADO® T. Proc® rotary lobe pump
- Medium: Hydrogel
- Capacity: 22 m³/h
- Pressure: 5 bar
- Temperature: 20 °C
- Additional information: Very shear-sensitive product